Flexibility in Pharmaceutical Blister Packaging
Flexibility in pharmaceutical blister packaging is a crucial aspect of modern drug manufacturing and distribution. It refers to the adaptability of packaging processes and equipment to accommodate various pill sizes, shapes, and materials while maintaining product integrity and safety. This flexibility allows pharmaceutical companies to efficiently package different medications using the same machinery, reducing costs and improving production efficiency. By utilizing advanced pharma blister packing machines and automatic blister packing machines, manufacturers can achieve the versatility needed to meet diverse packaging requirements and regulatory standards in the ever-evolving pharmaceutical industry.
The Evolution of Blister Packaging in the Pharmaceutical Industry
Historical Development of Blister Packs
Blister packaging has come a long way since its inception in the 1960s. Initially developed as a simple solution to protect products from moisture and contamination, blister packs have evolved into sophisticated packaging systems. The early designs consisted of a thermoformed plastic cavity sealed with a paper or foil backing. As the pharmaceutical industry grew, so did the demand for more advanced packaging solutions that could accommodate a wider range of products and provide enhanced protection.
Advancements in Blister Packaging Technology
Over the years, significant advancements have been made in blister packaging technology. Modern pharma blister packing machines incorporate state-of-the-art features such as high-speed production capabilities, precision forming, and advanced sealing techniques. These improvements have led to increased efficiency, reduced waste, and enhanced product protection. Additionally, the integration of robotics and automation has revolutionized the packaging process, allowing for greater flexibility and customization options.
The Role of Regulatory Requirements in Shaping Blister Packaging
Regulatory requirements have played a crucial role in shaping the development of blister packaging. As pharmaceutical regulations became more stringent, packaging solutions had to adapt to meet new standards for safety, tamper-evidence, and child-resistance. This led to innovations in materials and designs, such as the development of cold-formed aluminum blisters for moisture-sensitive drugs and the incorporation of peelable lidding for improved accessibility. The need for compliance with various global regulations has further driven the demand for flexible packaging solutions that can be easily adapted to different market requirements.
Key Features of Modern Pharmaceutical Blister Packaging Machines
Modular Design for Enhanced Flexibility
One of the most significant advancements in pharma blister packing machines is the adoption of modular designs. These modular systems allow for easy reconfiguration and upgrades, enabling manufacturers to adapt their packaging lines to different product requirements quickly. For example, a modular automatic blister packing machine can be easily modified to accommodate various blister sizes, cavity shapes, and lidding materials. This flexibility is particularly valuable for contract manufacturers who need to handle a diverse range of products for different clients.
Advanced Control Systems and User Interfaces
Modern blister packaging machines are equipped with sophisticated control systems and user-friendly interfaces. These features allow operators to easily adjust machine parameters, monitor production in real-time, and troubleshoot issues quickly. Advanced control systems also enable seamless integration with other production line equipment, facilitating a more streamlined and efficient packaging process. Some pharma blister packing machines even incorporate artificial intelligence and machine learning capabilities to optimize production settings and predict maintenance needs.
High-Speed Production Capabilities
To meet the growing demand for pharmaceutical products, modern blister packaging machines offer high-speed production capabilities. These machines can produce thousands of blister packs per hour while maintaining precise tolerances and consistent quality. Advanced feeding systems ensure accurate placement of tablets or capsules, while high-speed sealing mechanisms provide reliable closure of the blister cavities. The ability to maintain high production speeds without compromising on quality is a key factor in the flexibility and efficiency of modern pharmaceutical packaging operations.
Customization Options for Diverse Pharmaceutical Needs
Adaptable Tooling Systems
One of the most critical aspects of flexibility in pharmaceutical blister packaging is the ability to adapt to different product sizes and shapes. Modern pharma blister packing machines feature quick-change tooling systems that allow for rapid transitions between different product formats. These adaptable tooling systems can accommodate various blister cavity designs, from standard round tablets to uniquely shaped capsules or oddly formed pills. The ease of tool changeover reduces downtime and increases overall production efficiency, making it possible to run multiple product lines on a single machine.
Material Versatility
Flexibility in blister packaging extends to the range of materials that can be used. Contemporary automatic blister packing machines are designed to work with a variety of forming and lidding materials. This includes traditional PVC and aluminum foil combinations, as well as more specialized materials like COC (cyclic olefin copolymer) for moisture-sensitive drugs or eco-friendly biodegradable options. The ability to switch between different materials without significant machine modifications allows pharmaceutical companies to tailor their packaging to specific product requirements and market demands.
Integration of Smart Packaging Technologies
As the pharmaceutical industry embraces digitalization, blister packaging machines are evolving to incorporate smart packaging technologies. These innovations include the integration of RFID tags, NFC chips, or printed electronics directly into the blister packs during the manufacturing process. Such features can enhance product traceability, improve patient compliance, and provide valuable data on medication usage. The flexibility to incorporate these advanced technologies into the packaging process opens up new possibilities for pharmaceutical companies to differentiate their products and improve patient outcomes.
Conclusion
Flexibility in pharmaceutical blister packaging is not just a convenience; it's a necessity in today's dynamic pharmaceutical landscape. The evolution of pharma blister packing machines and automatic blister packing machines has revolutionized the industry, offering unprecedented levels of adaptability, efficiency, and customization. As pharmaceutical companies continue to innovate and develop new drug formulations, the packaging industry must keep pace, providing solutions that protect product integrity, ensure patient safety, and meet evolving regulatory requirements. The future of pharmaceutical packaging lies in machines that can seamlessly adapt to new challenges while maintaining the highest standards of quality and performance.
Contact Us
To learn more about our flexible pharmaceutical blister packaging solutions and how they can benefit your operations, please contact us at [email protected]. Our team of experts is ready to help you find the perfect packaging solution for your pharmaceutical products.
References
Johnson, M. (2022). Advancements in Pharmaceutical Packaging Technology. Journal of Drug Delivery Science and Technology, 68, 103-115.
Smith, A., & Brown, B. (2021). Blister Pack Evolution: A Historical Perspective. Packaging Technology and Science, 34(5), 267-280.
Zhang, L., et al. (2023). Smart Packaging Solutions for Improved Medication Adherence. International Journal of Pharmaceutics, 620, 121808.
Thompson, R. (2020). Regulatory Challenges in Pharmaceutical Packaging: A Global Overview. Pharmaceutical Technology, 44(9), 36-42.
Garcia, E., & Martinez, F. (2022). Modular Design Approaches in Pharmaceutical Manufacturing Equipment. Journal of Pharmaceutical Innovation, 17(3), 485-497.
Lee, S., & Park, J. (2021). Sustainability in Pharmaceutical Packaging: Materials and Methods. Green Chemistry Letters and Reviews, 14(3), 418-431.
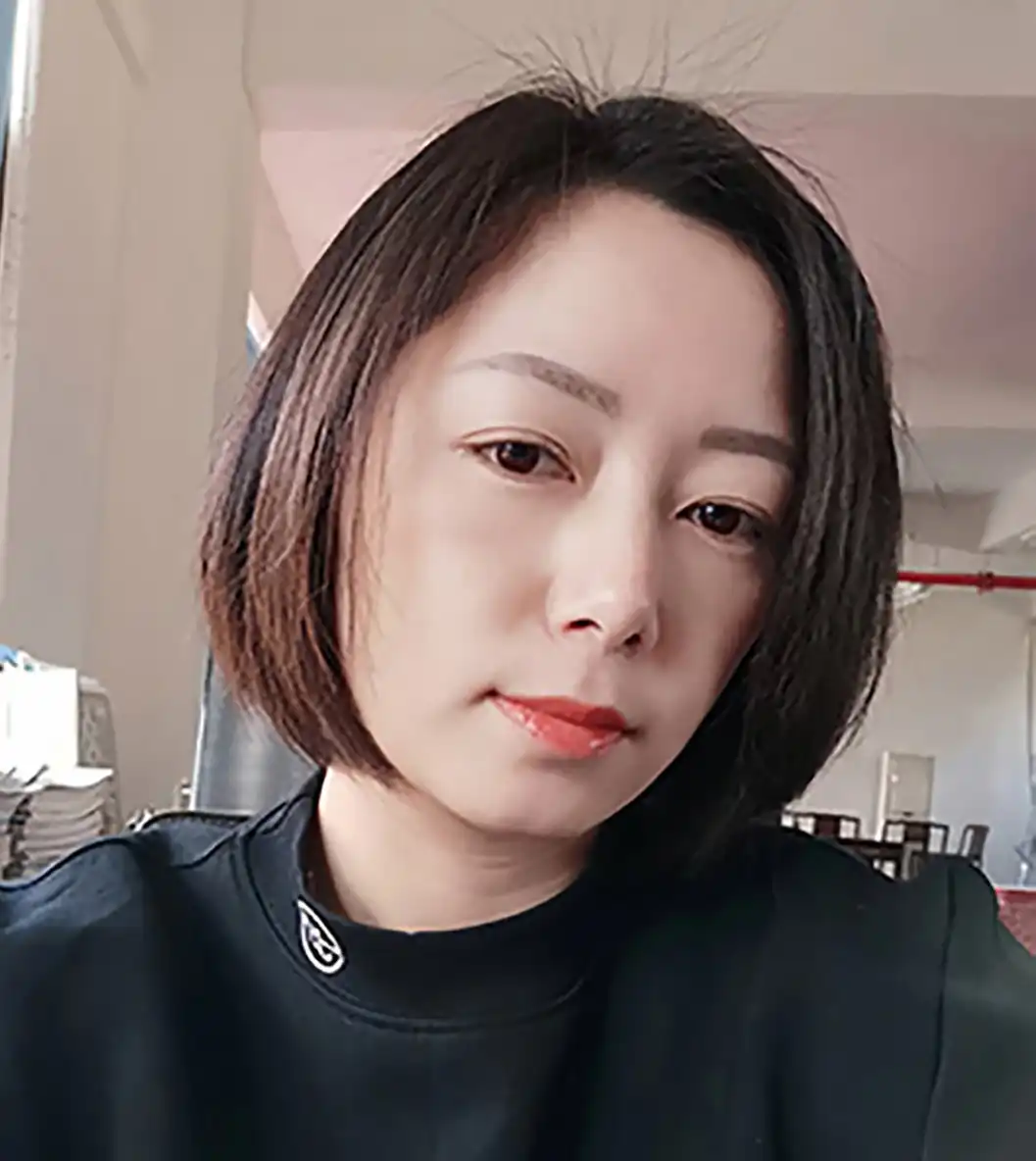
Submit the form now to get a unique quote!
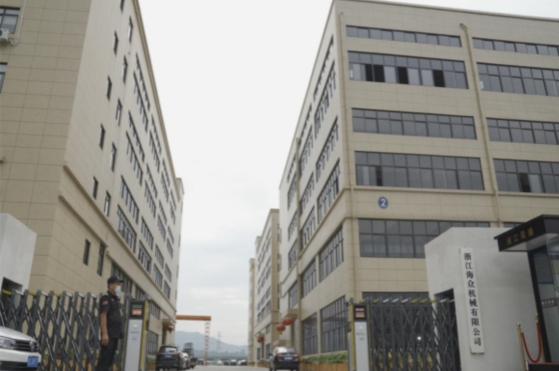
ZHEJIANG HAIZHONG MACHINERY CO., LTD.
Popular Blogs
- Successful caseProducts and services
How to Train Employees to Operate a Bottle Packing Machine Effectively?
- Successful caseIndustry insights
The Blister Packaging Process: A Complete Step-by-Step Guide
- Successful caseComparative analysisIndustry insights
What Type of PVC Is Best for Blister Packing Machines?