Alu-Alu blisters and Alu-PVC blisters are two popular packaging options in the pharmaceutical industry, each with distinct characteristics. Alu-Alu blisters consist of aluminum foil for both the forming and lidding materials, offering superior moisture and light protection. In contrast, Alu-PVC blisters use a PVC forming film with an aluminum lidding foil, providing a balance between protection and cost-effectiveness. The choice between these packaging types depends on factors such as product sensitivity, shelf life requirements, and environmental considerations. Understanding these differences is crucial for selecting the appropriate blister machine packing solution for pharmaceutical products.
Alu-Alu Blisters vs. Alu-PVC Blisters: What are the Differences
Understanding Blister Packaging Technology
The Evolution of Blister Packaging
Blister packaging has revolutionized the pharmaceutical industry since its inception. This innovative packaging method originated in the 1960s and has since undergone significant advancements. Initially designed to protect pills from moisture and contamination, blister packs have evolved to meet increasingly stringent regulatory requirements and consumer demands. The technology behind blister packaging machinery has progressed rapidly, allowing for higher production speeds, improved quality control, and enhanced customization options.
Components of Blister Packaging
Modern blister packages comprise two primary components: the forming film and the lidding material. The forming film, typically made from plastic or aluminum, creates cavities or "blisters" that house individual doses of medication. The lidding material, often aluminum foil or a combination of materials, seals the package. Advanced blister packaging equipment utilizes precise thermoforming and sealing processes to ensure product integrity and tamper-evidence. Understanding these components is crucial for pharmaceutical companies seeking to optimize their packaging solutions.
Blister Machine Packing Process
The blister machine packing process is a marvel of engineering efficiency. It begins with the feeding of the forming material into the machine, where it's heated and molded into the desired blister shape. Next, the product is carefully placed into these formed cavities. The filling process can be manual for small-scale operations or fully automated for high-volume production. Once filled, the blisters are sealed with the lidding material using heat and pressure. Finally, the sealed blisters are cut and separated into individual units or strips. This seamless process, facilitated by sophisticated blister packaging machinery, ensures consistent quality and protection for pharmaceutical products.
Comparative Analysis of Alu-Alu and Alu-PVC Blisters
Material Composition and Properties
Alu-Alu blisters boast a composition of aluminum for both the forming and lidding materials. This dual-aluminum structure provides exceptional barrier properties against moisture, light, and gases. The malleability of aluminum allows for deep-drawing capabilities, accommodating various pill shapes and sizes. On the other hand, Alu-PVC blisters utilize a polyvinyl chloride (PVC) forming film with an aluminum lidding foil. PVC offers good thermoforming characteristics and clarity, allowing visual inspection of the packaged product. However, its barrier properties are inferior to aluminum, particularly concerning moisture protection.
Protection and Shelf Life
When it comes to protection and shelf life, Alu-Alu blisters excel. The impermeable nature of aluminum on both sides creates a virtually hermetic seal, significantly extending the shelf life of moisture-sensitive medications. This makes Alu-Alu blisters ideal for hygroscopic drugs or those requiring long-term storage. Alu-PVC blisters, while offering adequate protection for many products, are more susceptible to moisture ingress through the PVC layer. Consequently, they may not be suitable for highly sensitive pharmaceuticals or those intended for distribution in high-humidity environments. The choice between these packaging types often hinges on the specific stability requirements of the drug product and the compatibility with a high speed blister packing machine.
Cost Considerations and Sustainability
Cost is a significant factor in the selection of blister packaging materials. Alu-PVC blisters generally offer a more economical solution due to the lower cost of PVC compared to aluminum. This cost advantage has contributed to the widespread use of Alu-PVC blisters in the pharmaceutical industry. However, the increasing focus on sustainability presents new considerations. Aluminum, being infinitely recyclable, gives Alu-Alu blisters an edge in environmental friendliness. PVC, while recyclable, poses more challenges in the recycling process. As environmental regulations tighten globally, pharmaceutical companies are increasingly weighing the long-term sustainability benefits against short-term cost savings when choosing between Alu-Alu and Alu-PVC blister packaging.
Optimizing Blister Packaging Solutions
Customization and Innovation in Blister Design
The pharmaceutical packaging landscape is constantly evolving, driven by the need for enhanced product protection, patient compliance, and brand differentiation. Innovative blister designs now incorporate features such as child-resistant mechanisms, senior-friendly openings, and integrated desiccants. Advanced blister packaging equipment allows for intricate shapes and sizes, catering to unique dosage forms like orally disintegrating tablets or oddly shaped capsules. Some cutting-edge designs even incorporate electronic components for tracking medication adherence. These customizations not only improve functionality but also offer opportunities for brand distinction in a competitive market.
Quality Control and Regulatory Compliance
Ensuring the quality and safety of pharmaceutical packaging is paramount. Modern blister packaging machinery incorporates sophisticated quality control systems, including vision inspection technologies and leak detection mechanisms. These systems can identify defects such as incomplete seals, missing tablets, or foreign particles, ensuring that only perfect packages reach consumers. Moreover, compliance with regulatory standards like cGMP (current Good Manufacturing Practices) is crucial. Blister packaging equipment manufacturers are increasingly focusing on designing machines that facilitate compliance, with features like data logging, traceability, and clean-room compatibility. This integration of quality control and regulatory compliance in the packaging process is essential for maintaining product integrity and consumer trust.
Future Trends in Blister Packaging Technology
The future of blister packaging is shaped by emerging technologies and changing market demands. One notable trend is the integration of smart packaging technologies. RFID tags and NFC chips embedded in blister packs can provide real-time tracking, authentication, and patient engagement features. Another area of innovation is in sustainable materials. Biodegradable plastics and plant-based polymers are being explored as eco-friendly alternatives to traditional PVC. Additionally, advancements in blister packaging machinery are focusing on increased flexibility and faster changeovers to meet the growing demand for personalized medicine and smaller batch sizes. These trends indicate a future where blister packaging will not only protect products but also actively contribute to patient care and environmental sustainability.
Conclusion
The choice between Alu-Alu and Alu-PVC blisters depends on various factors including product sensitivity, regulatory requirements, and cost considerations. While Alu-Alu offers superior protection, Alu-PVC provides a cost-effective solution for less sensitive products. As the pharmaceutical industry evolves, innovations in blister packaging equipment and materials continue to expand the possibilities for product protection and patient convenience. Companies must carefully evaluate their specific needs to select the optimal blister packaging solution, balancing performance, cost, and sustainability.
Contact Us
For expert guidance on selecting and implementing the right blister packaging solution for your pharmaceutical products, contact Zhejiang Haizhong Machinery Co.,Ltd. at [email protected]. Our team of specialists is ready to help you navigate the complexities of pharmaceutical packaging and find the perfect solution for your unique needs.
References
Pilchik, R. (2000). Pharmaceutical blister packaging, Part I: Rationale and materials. Pharmaceutical Technology, 24(11), 68-78.
Forcinio, H. (2014). Blister packaging: Protecting products and enhancing compliance. Pharmaceutical Technology, 38(9), 36-40.
Lockhart, H., & Paine, F. A. (2019). Packaging of pharmaceuticals and healthcare products. Springer Science & Business Media.
Bauer, E. J. (2009). Pharmaceutical packaging handbook. CRC Press.
Mehta, K. (2018). Innovations in pharmaceutical packaging. Journal of Drug Delivery and Therapeutics, 8(3), 85-90.
Zadbuke, N., Shahi, S., Gulecha, B., Padalkar, A., & Thube, M. (2013). Recent trends and future of pharmaceutical packaging technology. Journal of Pharmacy & Bioallied Sciences, 5(2), 98-110.
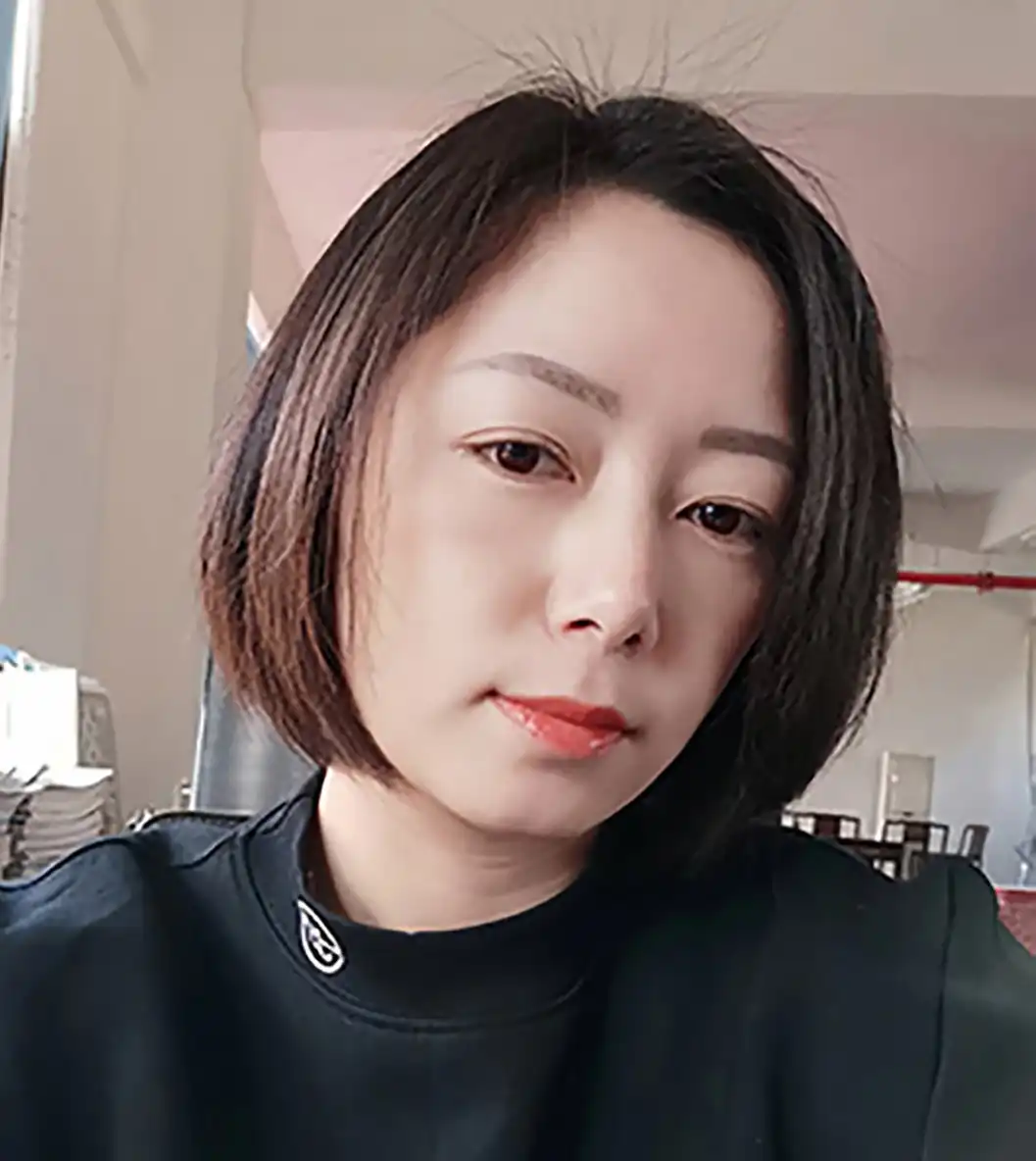
Submit the form now to get a unique quote!
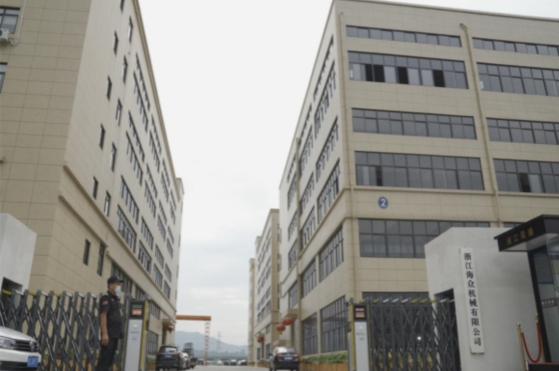
ZHEJIANG HAIZHONG MACHINERY CO., LTD.
Popular Blogs
- Successful caseProducts and services
How to Train Employees to Operate a Bottle Packing Machine Effectively?
- Successful caseIndustry insights
The Blister Packaging Process: A Complete Step-by-Step Guide
- Successful caseComparative analysisIndustry insights
What Type of PVC Is Best for Blister Packing Machines?