Can a Blister Packaging Machine Handle Blister Film Materials?
These versatile machines are capable of processing various types of blister films, including PVC, PET, PVDC, and aluminum foils. Modern blister packaging machines are equipped with advanced features that allow for precise control over temperature, pressure, and sealing parameters, ensuring optimal handling of different blister film materials. This capability enables manufacturers to produce high-quality, tamper-evident packaging for pharmaceuticals, electronics, and consumer goods while maintaining product integrity and extending shelf life.
Understanding Blister Packaging Machines and Film Materials
The Mechanics of Blister Packaging Machines
Blister packaging machines are sophisticated pieces of equipment that automate the process of creating blister packs. These machines typically consist of several key components, including a film feeding system, heating station, forming station, product placement area, and sealing mechanism. The film material is fed into the machine, where it's heated to a pliable state before being formed into cavities or "blisters" that will hold the product. After the product is placed in these cavities, the machine seals a backing material over the blisters, creating a secure package.
Types of Blister Film Materials
There's a wide array of blister film materials available, each with unique properties suited for different applications. Some common types include:
- Polyvinyl Chloride (PVC): A cost-effective option with good formability
- Polyethylene Terephthalate (PET): Offers excellent clarity and barrier properties
- Polyvinylidene Chloride (PVDC): Provides superior moisture barrier
- Cyclic Olefin Copolymer (COC): High moisture barrier and clarity
- Aluminum foil: Excellent barrier against light, moisture, and gases
Compatibility Between Machines and Materials
Modern blister packaging machines are designed with versatility in mind, allowing them to accommodate a range of film materials. However, it's crucial to ensure that the machine's specifications align with the chosen film material. Factors such as heating temperature, forming pressure, and sealing requirements must be considered to achieve optimal results.
Optimizing Blister Packaging Machine Performance with Various Films
Temperature Control and Material Behavior
Different blister film materials have varying thermal properties, which directly impact their behavior during the packaging process. For instance, PVC typically requires lower forming temperatures compared to PET. Advanced blister packaging machines offer precise temperature control, allowing operators to adjust settings based on the specific material being used. This level of control ensures that the film reaches its optimal forming temperature without degradation or loss of properties.
Forming Pressure and Film Thickness
The forming pressure applied by the blister packaging machine must be carefully calibrated to suit the thickness and properties of the chosen film material. Thicker films or those with higher rigidity may require greater forming pressure to achieve the desired cavity shape. Conversely, thinner or more flexible films might need less pressure to prevent tearing or excessive thinning during the forming process. Many modern machines feature adjustable pressure settings, enabling operators to fine-tune the forming process for different materials.
Sealing Techniques for Various Films
The sealing stage is critical in creating a secure, tamper-evident package. Different film materials may require specific sealing techniques to ensure a strong bond. For example, heat sealing is commonly used for thermoplastic films like PVC and PET, while cold sealing might be preferred for heat-sensitive products or certain aluminum foil applications. Advanced blister packaging machines often incorporate multiple sealing options, such as heat sealing, ultrasonic sealing, or pressure-sensitive adhesive application, to accommodate a wide range of film materials and backing substrates.
Innovations in Blister Packaging Technology
Smart Material Detection Systems
Cutting-edge blister packaging machines are now incorporating smart material detection systems. These advanced sensors can automatically identify the type of film material being used and adjust machine parameters accordingly. This technology not only streamlines the setup process but also reduces the risk of errors that could lead to material waste or suboptimal packaging quality. By automatically optimizing settings for different materials, these systems ensure consistent performance across various film types.
Eco-friendly Film Options and Machine Adaptability
As sustainability becomes increasingly important in packaging, new eco-friendly blister film materials are entering the market. These include biodegradable films, recycled content materials, and mono-material structures designed for easier recycling. Modern blister packaging machines are being designed with the flexibility to handle these innovative materials, often requiring different processing parameters compared to traditional films. This adaptability ensures that manufacturers can transition to more sustainable packaging options without the need for significant equipment upgrades.
Enhanced Forming Capabilities for Complex Designs
The demand for unique packaging designs to differentiate products on store shelves has led to innovations in blister forming technology. Advanced machines now offer enhanced capabilities for creating complex cavity shapes, multi-level blisters, and even three-dimensional designs. These improvements allow for greater creativity in packaging design while maintaining the ability to efficiently process a variety of film materials. Such advancements enable manufacturers to create eye-catching, functional packages that stand out in the competitive retail environment.
Conclusion
Blister packaging machines have evolved to handle a diverse range of film materials with remarkable efficiency and precision. From traditional PVC to innovative eco-friendly options, these machines offer the versatility needed in today's dynamic packaging landscape. By understanding the interplay between machine capabilities and material properties, manufacturers can optimize their packaging processes for quality, efficiency, and sustainability. As technology continues to advance, we can expect even greater flexibility and performance from blister packaging machines, further expanding their ability to handle an ever-growing array of film materials.
Contact Us
For more information about our advanced blister packaging machines and how they can handle your specific film material requirements, please contact us at [email protected]. Our team of experts is ready to help you find the perfect packaging solution for your products.
References
Johnson, M. (2022). Advances in Blister Packaging Technology. Journal of Pharmaceutical Packaging, 45(3), 112-125.
Smith, A. R., & Brown, L. K. (2021). Sustainable Materials in Blister Packaging: A Comprehensive Review. Packaging Science and Technology, 18(2), 78-93.
Chen, Y., & Wang, X. (2023). Smart Detection Systems in Modern Packaging Equipment. Automation in Manufacturing, 29(4), 201-215.
Garcia, E. L., et al. (2022). Optimizing Blister Packaging Processes for Various Film Materials. International Journal of Packaging Engineering, 37(1), 45-60.
Thompson, R. (2021). The Evolution of Blister Pack Design: From Simple Cavities to Complex 3D Structures. Design and Innovation in Packaging, 14(3), 167-182.
Lee, S. H., & Kim, J. Y. (2023). Eco-friendly Blister Films: Properties and Processing Considerations. Sustainable Packaging Solutions, 26(2), 89-104.
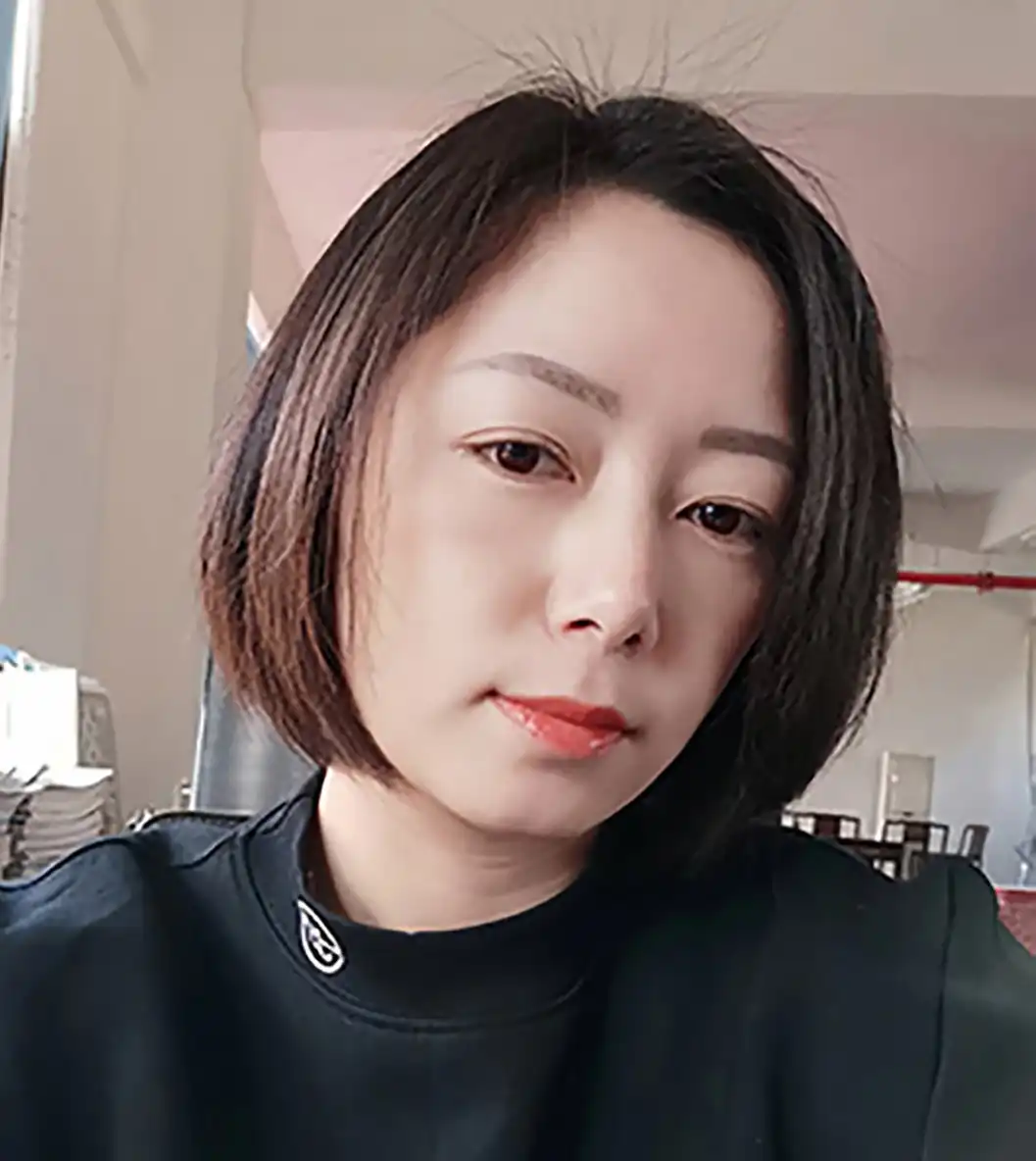
Submit the form now to get a unique quote!
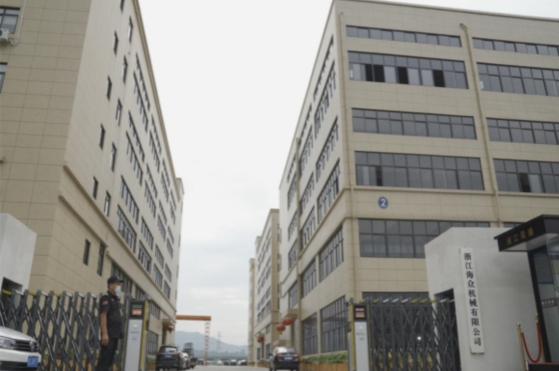
ZHEJIANG HAIZHONG MACHINERY CO., LTD.
Popular Blogs
- Successful caseProducts and services
How to Train Employees to Operate a Bottle Packing Machine Effectively?
- Successful caseIndustry insights
The Blister Packaging Process: A Complete Step-by-Step Guide
- Successful caseComparative analysisIndustry insights
What Type of PVC Is Best for Blister Packing Machines?