How does a Flow Pack Machine Work?
A flow pack machine, also known as a pillow packing machine, is a versatile packaging solution that efficiently wraps products in a continuous process. It uses a roll of film to envelop items on a conveyor belt, forming a pillow-shaped package around each product. The machine then seals and cuts the film, creating individual packages. This automated system is widely used in various industries, including food, pharmaceuticals, and consumer goods, to enhance productivity and ensure product protection. Flow pack machines offer a streamlined approach to packaging, combining speed, efficiency, and reliability to meet the demands of modern production lines.
The Core Components and Mechanics of Flow Pack Machines
Film Feeding and Forming System
At the core of every flow pack machine lies the film feeding and forming system, a crucial component that ensures smooth packaging operations. This system begins by unwinding a large roll of packaging film and precisely guiding it through a network of rollers. As the film advances, it passes over a forming collar, gradually taking the shape of a tube. This transformation from a flat sheet into a three-dimensional structure is essential for securely enclosing the product before sealing and cutting.
Product Infeed and Spacing
The product infeed mechanism plays a vital role in ensuring a consistent and efficient flow of items into the packaging process. Typically, it consists of a conveyor system designed to regulate the timing and spacing of products as they enter the pillow packing machine. By maintaining precise spacing, the system prevents issues such as overcrowding or irregular gaps, which could disrupt the packaging sequence. This careful alignment ensures that each item is accurately positioned for wrapping, contributing to smooth and reliable operation.
Sealing and Cutting Mechanisms
Once the product is fully enclosed by the film, the packaging process moves to the sealing and cutting stages. Horizontal seal bars press firmly to create the front and back seals, ensuring the package is securely closed. Simultaneously, a vertical seal forms along the length of the film, maintaining structural integrity. A cutting mechanism, often a rotating blade or heated wire, then slices through the film, separating each package from the continuous tube. These steps work seamlessly together to produce neatly sealed, precisely cut, and shipment-ready products.
Advanced Features and Customization Options
Intelligent Control Systems
Modern flow pack machines come with advanced control systems that offer precise adjustments and real-time monitoring. Equipped with user-friendly touch-screen interfaces, operators can easily fine-tune critical parameters like sealing temperature, film tension, and cutting frequency. These intelligent systems also provide instant diagnostics and detailed production data, allowing for quick troubleshooting and process optimization. By enhancing efficiency and minimizing downtime, they help maintain consistent packaging quality and improve overall operational productivity.
Adaptable Packaging Formats
Flow pack machines provide exceptional versatility in packaging formats, accommodating styles such as pillow packs, gusseted bags, and stand-up pouches. This adaptability makes them ideal for packaging a diverse range of products, from chocolates and snacks to electronics and household goods. Their ability to switch between formats quickly enables manufacturers to keep pace with shifting market trends, meet consumer preferences, and efficiently handle different product sizes without extensive downtime or costly reconfigurations.
Integration with Auxiliary Equipment
For a complete packaging solution, flow pack machines can seamlessly integrate with various auxiliary equipment, enhancing both efficiency and quality control. These additions may include date coders for printing batch numbers and expiration dates, metal detectors to identify contaminants, and checkweighers to verify product weight accuracy. By incorporating these systems, manufacturers ensure that each package is properly labeled, inspected, and compliant with industry standards before reaching consumers, reducing errors and maintaining product integrity.
Optimizing Performance and Maintenance
Film Selection and Management
Choosing the right packaging film is crucial for optimal machine performance. Factors such as film thickness, material composition, and barrier properties must be considered. Proper film management, including tension control and alignment, ensures smooth operation and reduces the risk of packaging defects. Regular monitoring of film quality and storage conditions is essential for maintaining consistent packaging results.
Regular Maintenance Protocols
To keep a flow pack machine running at peak efficiency, regular maintenance is indispensable. This includes routine cleaning of sealing bars and forming collars, lubrication of moving parts, and inspection of electrical components. Implementing a preventative maintenance schedule can significantly reduce unexpected downtime and extend the machine's lifespan. Training operators in basic troubleshooting can also help address minor issues quickly and maintain productivity.
Performance Monitoring and Optimization
Continuous monitoring of machine performance is key to identifying areas for improvement. Many flow pack machines come equipped with data logging capabilities that track metrics such as packaging speed, film usage, and error rates. Analyzing this data can reveal opportunities for optimization, such as adjusting machine settings or redesigning product infeed systems. Regular performance reviews can lead to incremental improvements that boost overall packaging efficiency.
Conclusion
Flow pack machines represent a pinnacle of packaging technology, offering a blend of speed, versatility, and reliability. By understanding the intricate workings of these machines, from their core components to advanced features, manufacturers can harness their full potential. Regular maintenance, coupled with ongoing optimization efforts, ensures that flow pack machines continue to meet the evolving demands of modern production environments. As packaging needs grow more complex, these adaptable machines stand ready to deliver efficient, high-quality packaging solutions across diverse industries.
Contact Us
For more information about our flow pack machines and how they can revolutionize your packaging process, please contact us at [email protected]. Our team of experts is ready to help you find the perfect packaging solution for your specific needs.
References
Smith, J. (2021). "Advances in Flow Pack Technology for Food Packaging." Journal of Packaging Science and Technology, 15(3), 245-260.
Johnson, A. & Lee, S. (2020). "Optimizing Efficiency in Horizontal Flow Wrapping Machines." International Journal of Industrial Engineering, 28(2), 180-195.
Garcia, M. et al. (2022). "Sustainable Materials for Flow Pack Packaging: A Comprehensive Review." Sustainable Packaging Solutions, 7(4), 312-330.
Brown, R. (2019). "Integration of Quality Control Systems in Flow Pack Packaging Lines." Quality Assurance in Manufacturing, 12(1), 55-70.
Patel, N. & Wong, Y. (2023). "Industry 4.0 and Smart Packaging: The Role of Flow Pack Machines." Digital Transformation in Manufacturing, 9(2), 210-225.
Yamamoto, K. (2021). "Energy Efficiency Improvements in Modern Flow Pack Machines." Energy Conservation in Industrial Processes, 18(3), 290-305.
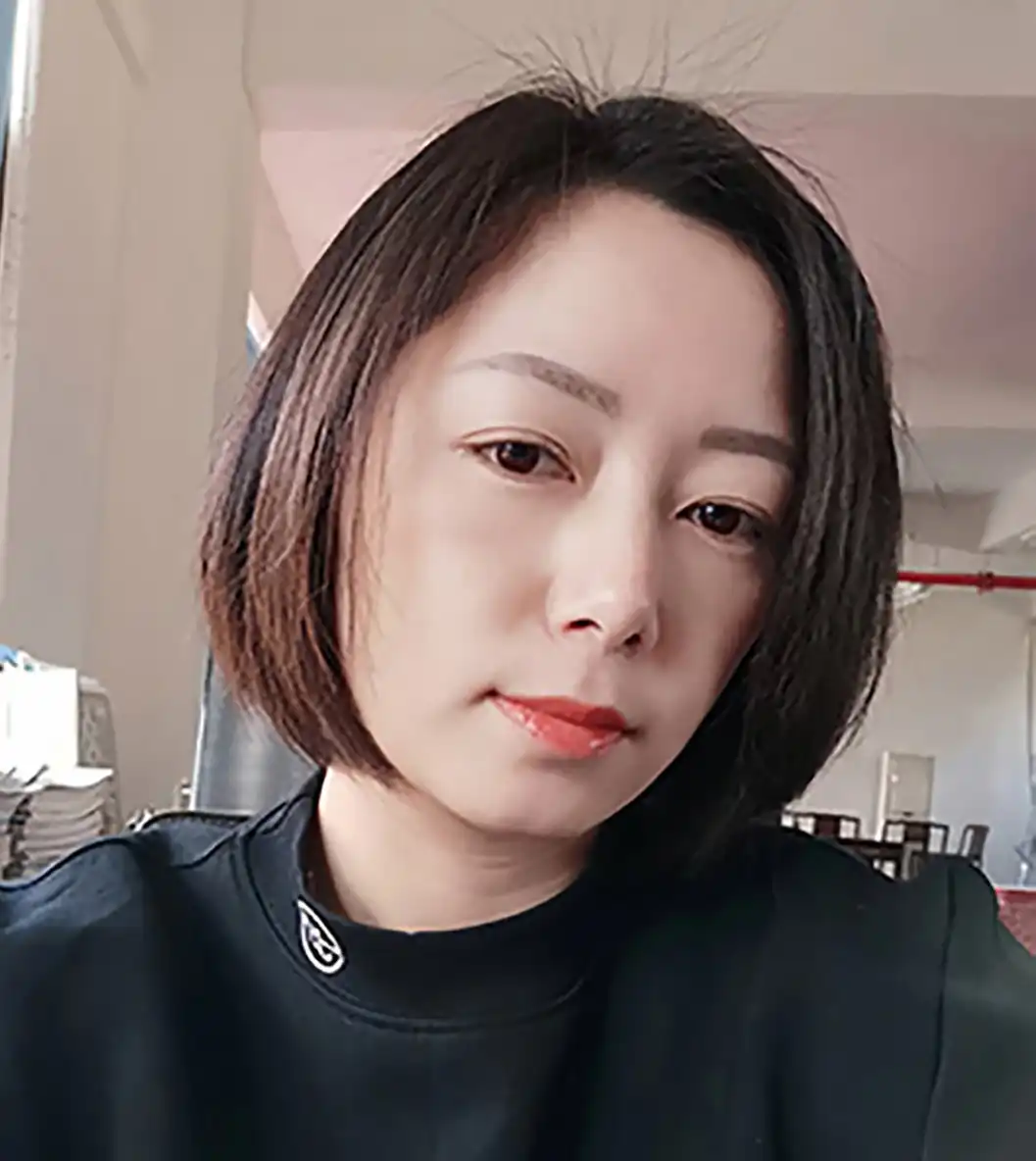
Submit the form now to get a unique quote!
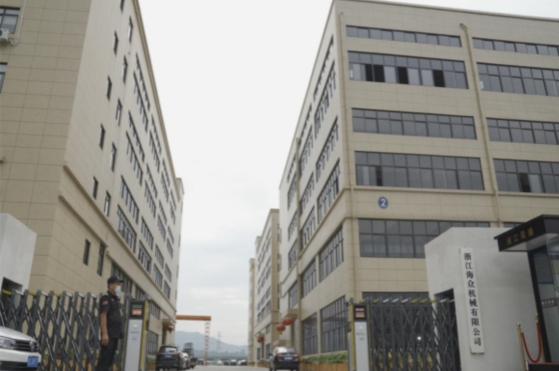
ZHEJIANG HAIZHONG MACHINERY CO., LTD.
Popular Blogs
- Successful caseProducts and services
How to Train Employees to Operate a Bread Packing Machine Effectively?
- Successful caseIndustry insights
The Blister Packaging Process: A Complete Step-by-Step Guide
- Successful caseComparative analysisIndustry insights
What Type of PVC Is Best for Blister Packing Machines?