How Does a Flow Packing Machine Work?
A flow packing machine, also known as a horizontal form-fill-seal (HFFS) machine, is an automated packaging system that creates sealed packages from a continuous roll of flexible film. The process involves forming a tube of packaging material, filling it with products, and sealing the ends to create individual packages. Flow packers utilize heat-sealing technology to create airtight, moisture-resistant packages for various products, including food items, pharmaceuticals, and consumer goods. These versatile machines can handle a wide range of package sizes and shapes, making them essential in modern packaging operations for their efficiency, speed, and ability to maintain product freshness.
The Anatomy of a Flow Packing Machine
Film Unwinding and Forming
The journey of packaging begins with the film roll holder, which securely holds the roll of packaging material. As the machine operates, it unwinds the film at a controlled rate, ensuring a consistent supply of packaging material. The film then passes through a series of rollers and guides, which help maintain proper tension and alignment.
Next, the film enters the forming box, a crucial component that shapes the flat film into a tube. The forming box typically consists of a metal collar that gradually folds the film around a forming tube. This process creates a continuous tube of packaging material, ready to receive the products.
Product Infeed and Filling
While the film is being formed into a tube, products are introduced into the machine through the infeed system. This can be a conveyor belt, vibrating feeder, or other specialized mechanisms designed to handle specific product types. The timing of product introduction is precisely synchronized with the film movement to ensure accurate placement within the package.
As the products enter the forming tube, they are guided into the film tube. The forming tube's length and diameter are customized based on the product size and desired package dimensions. Gravity assists in moving the products through the tube and into the waiting film envelope.
Sealing and Cutting
The sealing process is where the magic happens in flow wrapping. Horizontal sealing jaws close around the film tube, creating the front and back seals of each package. These jaws are typically heated to fuse the layers of film together, forming a strong, airtight seal.
Simultaneously, a vertical sealing mechanism creates the side seal of the package. This can be accomplished through various methods, including fin sealing or lap sealing, depending on the packaging requirements and film type.
Finally, a cutting device, often integrated with the horizontal sealing jaws, separates the individual packages. This precise cut ensures clean, uniform package edges and prepares the leading edge of the film for the next package.
Advanced Features and Technologies in Modern Flow Packers
Servo-Driven Systems
Contemporary flow packing machines often incorporate servo motors for enhanced precision and control. These motors allow for exact positioning of various machine components, resulting in improved package quality and reduced material waste. Servo-driven systems also enable quick changeovers between different product sizes or package formats, increasing the machine's versatility and efficiency.
The integration of servo technology extends to film feeding, product infeed, and sealing mechanisms. This level of control allows for smoother operation, higher speeds, and the ability to handle delicate or irregularly shaped products with greater care.
Intelligent Control Systems
Modern flow packers are equipped with sophisticated control systems that monitor and adjust various parameters in real-time. These systems utilize sensors and advanced algorithms to maintain optimal performance throughout the packaging process. For instance, they can automatically adjust sealing temperatures based on film thickness or ambient conditions, ensuring consistent seal quality.
Human-machine interfaces (HMIs) with intuitive touchscreen displays provide operators with easy access to machine settings, diagnostics, and production data. This level of control and monitoring contributes to improved overall equipment effectiveness (OEE) and reduced downtime.
Vision Systems and Quality Control
To ensure package integrity and product quality, many flow packing machines now incorporate vision systems. These high-speed cameras and image processing software can detect defects in packaging material, verify product presence and orientation, and inspect seal quality. When integrated with the machine's control system, vision technology can trigger automatic rejection of faulty packages or alert operators to potential issues.
Additionally, some advanced systems include in-line weight checking capabilities. This feature ensures that each package contains the correct amount of product, which is particularly crucial for industries with strict weight regulations, such as food and pharmaceuticals.
Applications and Industries Benefiting from Flow Packing Technology
Food and Beverage Sector
The food industry is one of the primary beneficiaries of flow packing technology. These machines are ideal for packaging a wide range of products, from snack foods and baked goods to fresh produce and frozen items. Flow packers can create modified atmosphere packaging (MAP) by injecting gases like nitrogen or carbon dioxide into the package, extending the shelf life of perishable foods.
In the confectionery sector, flow wrappers are used to package individual candies, chocolate bars, and other sweets. The high-speed capabilities of these machines make them perfect for handling the large volumes typical in this industry. Additionally, the ability to create attractive, eye-catching packages helps products stand out on retail shelves.
Pharmaceutical and Medical Devices
In the pharmaceutical industry, flow packing machines play a crucial role in packaging tablets, capsules, and medical devices. The hermetic seals created by these machines help protect sensitive products from moisture and contamination, ensuring product efficacy and safety. Many flow packers used in this sector are designed to meet stringent cleanroom requirements and comply with Good Manufacturing Practice (GMP) guidelines.
For medical devices, flow packing offers a cost-effective way to create sterile packaging. The machines can be integrated with sterilization processes, such as ethylene oxide treatment, to ensure that the packaged devices remain sterile until use.
Non-Food Consumer Goods
Flow packing technology extends beyond food and pharmaceuticals, finding applications in various consumer goods sectors. In the personal care and cosmetics industry, flow wrappers package items like soap bars, facial masks, and cosmetic pads. The machines' flexibility allows for the creation of single-use sachets, multi-packs, or larger family-size packages.
Hardware and DIY products also benefit from flow packing. Small components like screws, nails, and fittings can be efficiently packaged in user-friendly portions. The durability of flow-wrapped packages helps protect these items during transport and storage, while clear films allow for easy product identification.
Conclusion
Flow packing machines have revolutionized the packaging industry with their versatility, efficiency, and ability to create high-quality sealed packages. From their basic operating principles to advanced features like servo-driven systems and integrated quality control, these machines continue to evolve to meet the demands of various industries. As packaging technology advances, flow packers will likely see further improvements in speed, precision, and sustainability, cementing their place as a cornerstone of modern packaging operations.
Contact Us
For more information about our flow packing machines and how they can benefit your packaging operations, please contact us at [email protected]. Our team of experts at Zhejiang Haizhong Machinery Co., Ltd. is ready to help you find the perfect packaging solution for your specific needs.
References
Smith, J.R. (2019). Advanced Packaging Technologies in the Food Industry. Journal of Food Processing and Preservation, 43(2), 112-128.
Johnson, A.B. (2020). Innovations in Pharmaceutical Packaging Equipment. Pharmaceutical Technology, 44(5), 36-42.
Brown, C.D., & Davis, E.F. (2018). Energy Efficiency in Packaging Machinery. Packaging Technology and Science, 31(4), 213-225.
Lee, S.Y., & Kim, H.J. (2021). Quality Control Systems in Modern Packaging Lines. Journal of Applied Packaging Research, 13(1), 45-59.
Garcia, M.R., & Lopez, T.S. (2017). Servo Technology in Packaging Machines: A Comparative Study. International Journal of Advanced Manufacturing Technology, 89(5-8), 1845-1858.
Wilson, P.Q. (2022). Sustainability Trends in Flexible Packaging. Packaging Science and Technology, 35(3), 301-315.
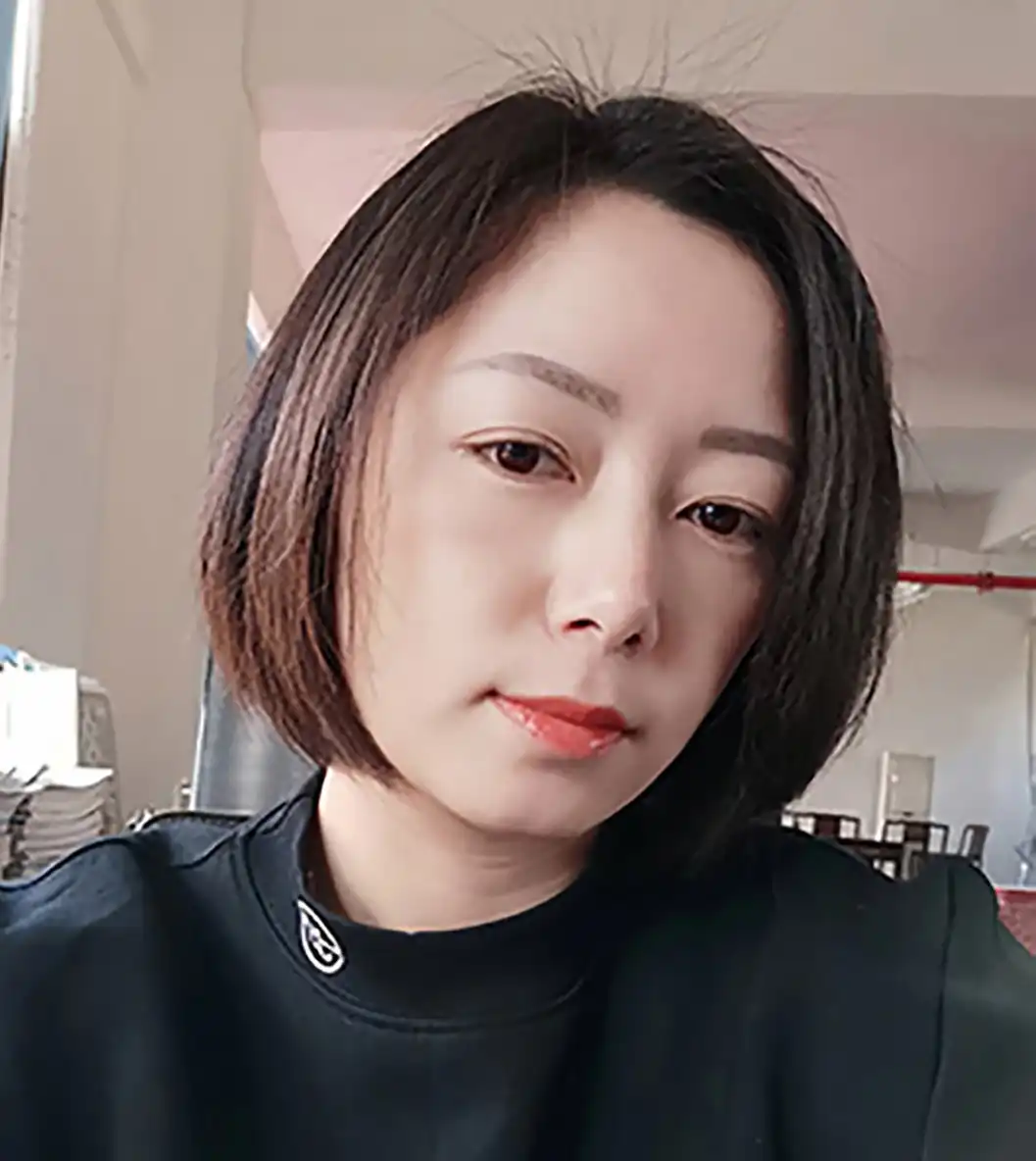
Submit the form now to get a unique quote!
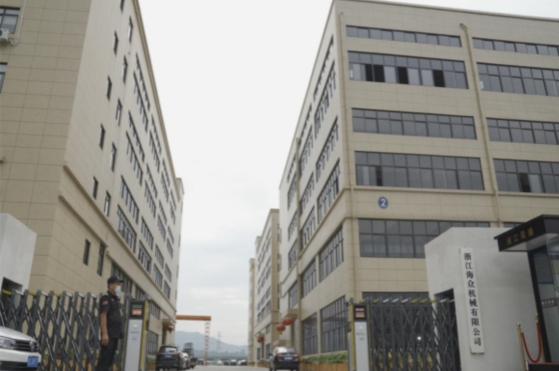
ZHEJIANG HAIZHONG MACHINERY CO., LTD.
Popular Blogs
- Successful caseProducts and services
How to Train Employees to Operate a Bottle Packing Machine Effectively?
- Successful caseIndustry insights
The Blister Packaging Process: A Complete Step-by-Step Guide
- Successful caseComparative analysisIndustry insights
What Type of PVC Is Best for Blister Packing Machines?