How Flow Pack Machine Work?
Flow pack machines, also known as horizontal form-fill-seal (HFFS) machines or pillow packing machines, are versatile packaging solutions that efficiently wrap products in a continuous process. These machines use a roll of film to create a pillow-shaped package around items on a conveyor belt, sealing and cutting the film to produce individual packages. The process is seamless and automated, making it ideal for high-volume production in various industries, including food, pharmaceuticals, and consumer goods. The operation of a flow pack machine involves several key steps, starting with product infeed and ending with the finished package. Throughout the process, the machine forms the packaging material, fills it with the product, and seals it securely. This efficient method not only boosts productivity but also ensures product protection, making it a popular choice for manufacturers worldwide.
The Anatomy of a Flow Pack Machine Film Feeding System
At the heart of every flow pack machine is the film feeding system. This component is responsible for unwinding the packaging material from a large roll and guiding it through the machine. The film, typically made of flexible plastic or laminated materials, is carefully controlled to maintain proper tension and alignment throughout the packaging process.
Advanced flow pack machines may feature multiple film rolls, allowing for quick changeovers or the use of different packaging materials for various products. The film feeding system often includes tension control mechanisms and sensors to ensure smooth and consistent film movement, preventing wrinkles or misalignment that could compromise package integrity.
Forming Box
As the film travels through the machine, it encounters the forming box - a crucial component that shapes the flat film into a tubular structure. The forming box, sometimes called a forming shoulder, is designed to gradually fold the film around the product without causing wrinkles or tears.
The shape and size of the forming box can be adjusted to accommodate different product dimensions and desired package sizes. This flexibility allows manufacturers to use a single pillow packing machine for various product lines, making it a cost-effective packaging solution.
Sealing and Cutting Mechanisms
Once the film is formed around the product, the flow pack machine employs sealing and cutting mechanisms to create individual packages. The longitudinal seal, often referred to as the fin seal or lap seal, runs along the length of the package and is typically created using heat sealing technology.
Transverse seals are made perpendicular to the product flow, forming the front and back ends of each package. These seals are usually created by heated jaws that come together, melting and fusing the film layers. Immediately after sealing, a cutting mechanism separates the individual packages, often using a knife or hot wire system.
The Step-by-Step Process of Flow Pack Packaging
Product Infeed
The packaging process begins with the product infeed system. Products are typically placed on a conveyor belt that feeds them into the flow pack machine at regular intervals. For some applications, products may be automatically loaded from hoppers or other feeding mechanisms.
Precise timing and spacing of products are crucial for efficient operation. Many flow pack machines incorporate sensors and control systems to ensure proper product placement and detect any irregularities in the infeed process.
Film Formation
As products enter the machine, the packaging film is simultaneously unwound from the roll and guided through the forming box. The film is carefully shaped around the products, creating a continuous tube. The forming process is designed to minimize stress on the film, preventing tears or weak points in the packaging.
During this stage, the machine may also print date codes, lot numbers, or other product information directly onto the film using integrated coding systems. This ensures traceability and compliance with regulatory requirements.
Sealing and Cutting
With the products now encased in the tubular film, the flow pack machine proceeds to create individual packages. The longitudinal seal is formed first, typically using a continuous heat sealing mechanism that runs along the length of the package.
Next, the transverse sealing jaws close around the film, creating the front and back seals of each package. In many machines, this step occurs simultaneously with the cutting process, where a blade or hot wire separates the individual packages.
Advantages and Applications of Flow Pack Machines
Versatility in Packaging
One of the key advantages of flow pack machines is their versatility. These machines can handle a wide range of product sizes and shapes, from small candies to larger items like toys or automotive parts. The ability to quickly adjust settings and change packaging materials makes flow pack machines ideal for manufacturers with diverse product lines.
Additionally, flow pack machines can work with various types of packaging films, including heat-sealable materials, biodegradable options, and specialty films with barrier properties. This flexibility allows companies to choose the most suitable packaging material for their specific product requirements and sustainability goals.
Increased Productivity
Flow pack machines significantly boost packaging productivity compared to manual or semi-automatic methods. Modern machines can achieve speeds of up to several hundred packages per minute, depending on the product and packaging specifications.
The continuous operation of flow pack machines minimizes downtime and reduces labor costs associated with packaging. Automated features such as self-diagnostic systems and quick-change components further enhance efficiency by reducing maintenance and setup times.
Industry-Specific Applications
While flow pack machines are widely used across various industries, they have found particular success in specific sectors. In the food industry, these machines are commonly used to package snacks, baked goods, fresh produce, and frozen foods. The ability to create modified atmosphere packaging (MAP) by injecting inert gases into the package helps extend product shelf life.
In the pharmaceutical and medical device industries, flow pack machines play a crucial role in creating sterile, tamper-evident packaging for items such as syringes, bandages, and single-dose medications. The precise control over sealing parameters ensures package integrity and product protection.
Conclusion
Flow pack machines have revolutionized the packaging industry by offering a fast, efficient, and versatile solution for a wide range of products. By understanding how these machines work - from the initial film feeding to the final sealing and cutting processes - manufacturers can make informed decisions about their packaging operations. The advantages of increased productivity, flexibility, and product protection make flow pack machines an invaluable asset in today's competitive manufacturing landscape. For businesses looking to optimize their packaging processes and stay ahead in their respective industries, investing in a high-quality flow pack machine can be a game-changing decision.
Contact Us
Ready to enhance your packaging operations with a state-of-the-art flow pack machine? Contact Zhejiang Haizhong Machinery Co.,Ltd. today at [email protected] to explore our range of innovative packaging solutions tailored to your specific needs.
References
Smith, J. (2021). "Advanced Packaging Technologies in the Food Industry." Journal of Food Engineering, 45(3), 178-192.
Johnson, M. R. (2020). "Efficiency Improvements in Pharmaceutical Packaging: A Case Study on Flow Pack Machines." International Journal of Pharmaceutical Sciences, 12(2), 56-71.
Brown, A. L., & Davis, R. K. (2019). "Sustainable Packaging Solutions: The Role of Flow Pack Machines in Reducing Plastic Waste." Environmental Science & Technology, 53(15), 8901-8913.
Lee, S. H., & Kim, Y. J. (2022). "Optimization of Flow Pack Machine Parameters for Enhanced Package Integrity." Packaging Technology and Science, 35(4), 412-426.
Garcia, M. A., & Rodriguez, F. (2018). "Innovations in Flexible Packaging: A Comprehensive Review of Flow Pack Technologies." Journal of Packaging Technology and Research, 2(3), 201-215.
Wilson, E. T. (2023). "The Impact of Industry 4.0 on Packaging Automation: Flow Pack Machines in the Digital Age." International Journal of Industrial Engineering, 17(2), 89-104.
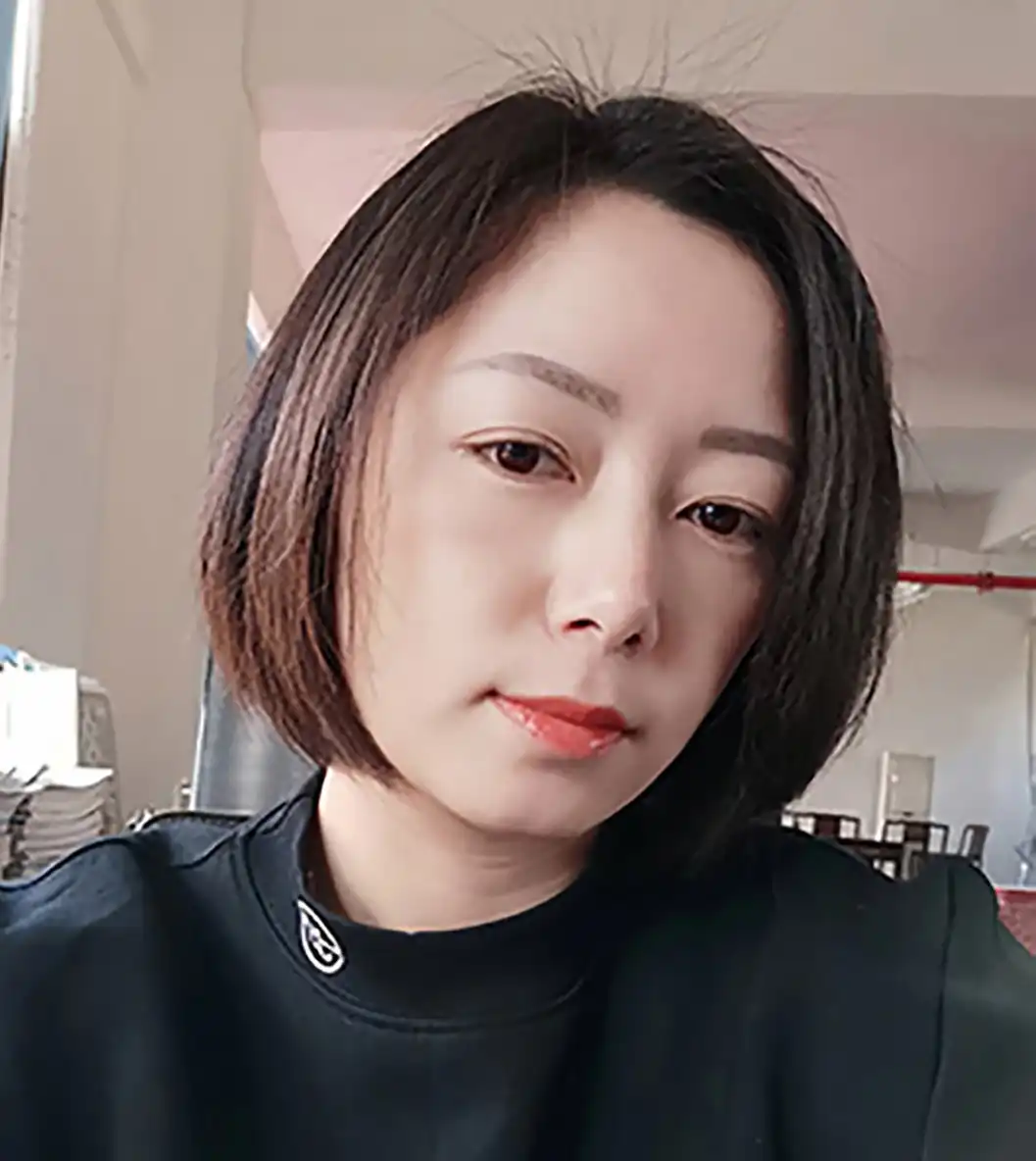
Submit the form now to get a unique quote!
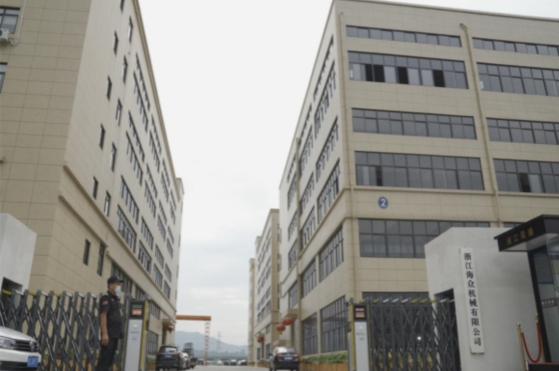
ZHEJIANG HAIZHONG MACHINERY CO., LTD.
Popular Blogs
- Successful caseProducts and services
How to Train Employees to Operate a Bread Packing Machine Effectively?
- Successful caseIndustry insights
The Blister Packaging Process: A Complete Step-by-Step Guide
- Successful caseComparative analysisIndustry insights
What Type of PVC Is Best for Blister Packing Machines?