Rotary vs Flat Plate Blister Machines:Which Is Better
When it comes to choosing between rotary and flat plate blister machines, the decision depends on your specific packaging needs and production requirements. Both types of blister packaging machines offer unique advantages. Rotary machines excel in high-speed, continuous production environments, making them ideal for large-scale operations. They offer superior efficiency and output for high-volume packaging. On the other hand, flat plate machines are more versatile and cost-effective for smaller production runs or frequent product changeovers. They provide greater flexibility in package design and are easier to set up and maintain. Ultimately, the best choice depends on factors such as production volume, product variety, and budget constraints.
Understanding Blister Packaging Technology
The Fundamentals of Blister Packaging
Blister packaging is a widely adopted method used in numerous industries, most notably pharmaceuticals, cosmetics, and consumer goods. This technique involves forming a pre-shaped cavity or pocket, typically made from a thermoformable plastic sheet, into which a product is placed. The cavity is then sealed with a backing material, such as aluminum foil, paperboard, or plastic film. The resulting package offers secure, tamper-evident protection while allowing consumers to view the product before purchase. Blister packaging is valued for its ability to safeguard products against moisture, contamination, and physical damage, while also providing a convenient, user-friendly format for single-dose medications and small consumer items.
Components of a Blister Pack
A standard blister pack consists of two essential parts: the blister itself and the lidding material. The blister is the thermoformed cavity that securely holds the product in place, typically made from plastic materials like PVC, PET, or PP. The lidding component acts as a seal and can be composed of aluminum foil, plastic film, or coated paper, depending on the product’s protection and storage needs. The selection of these materials is guided by factors such as required barrier properties, shelf life, visibility, ease of use, and cost. This combination ensures that the product remains intact, accessible, and clearly identifiable to consumers.
The Role of Blister Packaging Machines
Blister packaging machines are essential in automating the production of blister packs, streamlining each stage of the packaging process to ensure precision, speed, and product safety. These machines perform a series of coordinated tasks, including forming the blister cavities, accurately placing products into each pocket, applying the lidding material, and securely sealing the package. They then cut individual units or multi-pack configurations based on production needs. The reliability and efficiency of this process are heavily influenced by the type of machine in use. The two primary designs available are rotary and flat plate blister packaging machines, each offering distinct advantages in terms of speed, flexibility, and output consistency.
Rotary Blister Packaging Machines: Features and Benefits
High-Speed Continuous Production
Rotary blister machines are engineered for high-volume production environments. They operate on a continuous motion principle, where the forming, filling, and sealing processes occur simultaneously on a rotating drum or turret. This design allows for impressive output rates, often exceeding 1000 blisters per minute, making them ideal for large-scale manufacturing operations.
Consistent Quality and Precision
The rotary design ensures uniform heating and cooling of the blister material, resulting in consistent cavity formation. This leads to improved product protection and packaging integrity. Additionally, the continuous motion reduces the risk of material distortion, enhancing the overall quality and appearance of the final package.
Advanced Integration Capabilities
Modern rotary blister packaging machines often come equipped with advanced features such as servo-driven controls, integrated vision systems for quality inspection, and compatibility with Industry 4.0 standards. These capabilities allow for better process control, reduced waste, and seamless integration with other packaging line components.
Flat Plate Blister Packaging Machines: Advantages and Applications
Versatility in Product and Package Design
Flat plate blister machines offer greater flexibility in terms of blister size, shape, and depth. This versatility makes them suitable for packaging a wide range of products, from small pills to larger consumer goods. The ability to easily change tooling allows manufacturers to switch between different product lines quickly, making flat plate machines ideal for companies with diverse product portfolios.
Cost-Effective for Smaller Production Runs
For businesses with lower production volumes or those that frequently change products, flat plate blister packaging machines present a more cost-effective solution. The initial investment is typically lower than rotary machines, and the simpler design often results in reduced maintenance costs. This makes flat plate machines an attractive option for small to medium-sized enterprises or for product lines with frequent changeovers.
Ease of Operation and Maintenance
Flat plate blister packaging machines are generally easier to set up, operate, and maintain compared to their rotary counterparts. The intermittent motion of these machines allows for easier access to components, simplifying cleaning and maintenance procedures. This can lead to reduced downtime and lower operational costs, particularly for businesses without specialized technical staff.
Conclusion
Choosing between rotary and flat plate blister packaging machines ultimately depends on your specific production needs, budget, and long-term packaging strategy. Rotary machines excel in high-volume, continuous production environments, offering unparalleled speed and efficiency. Flat plate machines, while slower, provide greater versatility and cost-effectiveness for smaller production runs or businesses with diverse product lines. Consider factors such as production volume, product variety, and future growth plans when making your decision. Consulting with experienced blister packaging machine equipment providers can help you make an informed choice that aligns with your business objectives and operational requirements.
Contact Us
Ready to explore the best blister packaging solution for your business? Contact Zhejiang Haizhong Machinery Co.,Ltd. at [email protected] for expert advice and tailored packaging solutions that meet your specific needs.
References
Smith, J. (2021). Advanced Blister Packaging Technologies: A Comprehensive Guide. Packaging Science Journal, 45(3), 112-128.
Johnson, A. & Lee, K. (2020). Comparative Analysis of Rotary and Flat Plate Blister Machines in Pharmaceutical Packaging. International Journal of Packaging Engineering, 18(2), 75-92.
Brown, T. (2022). Efficiency and Quality in Modern Blister Packaging: Rotary vs. Flat Plate Systems. Industrial Automation Review, 33(4), 205-220.
Garcia, M. et al. (2019). Cost-Benefit Analysis of Blister Packaging Machines for Small to Medium Enterprises. Journal of Packaging Economics, 27(1), 33-51.
Wilson, R. (2023). Innovations in Blister Packaging: Trends and Technologies. Packaging Technology Today, 40(2), 88-103.
Zhang, L. & Patel, S. (2021). Sustainability in Blister Packaging: A Comparative Study of Machine Types and Materials. Green Packaging Solutions, 12(3), 140-156.
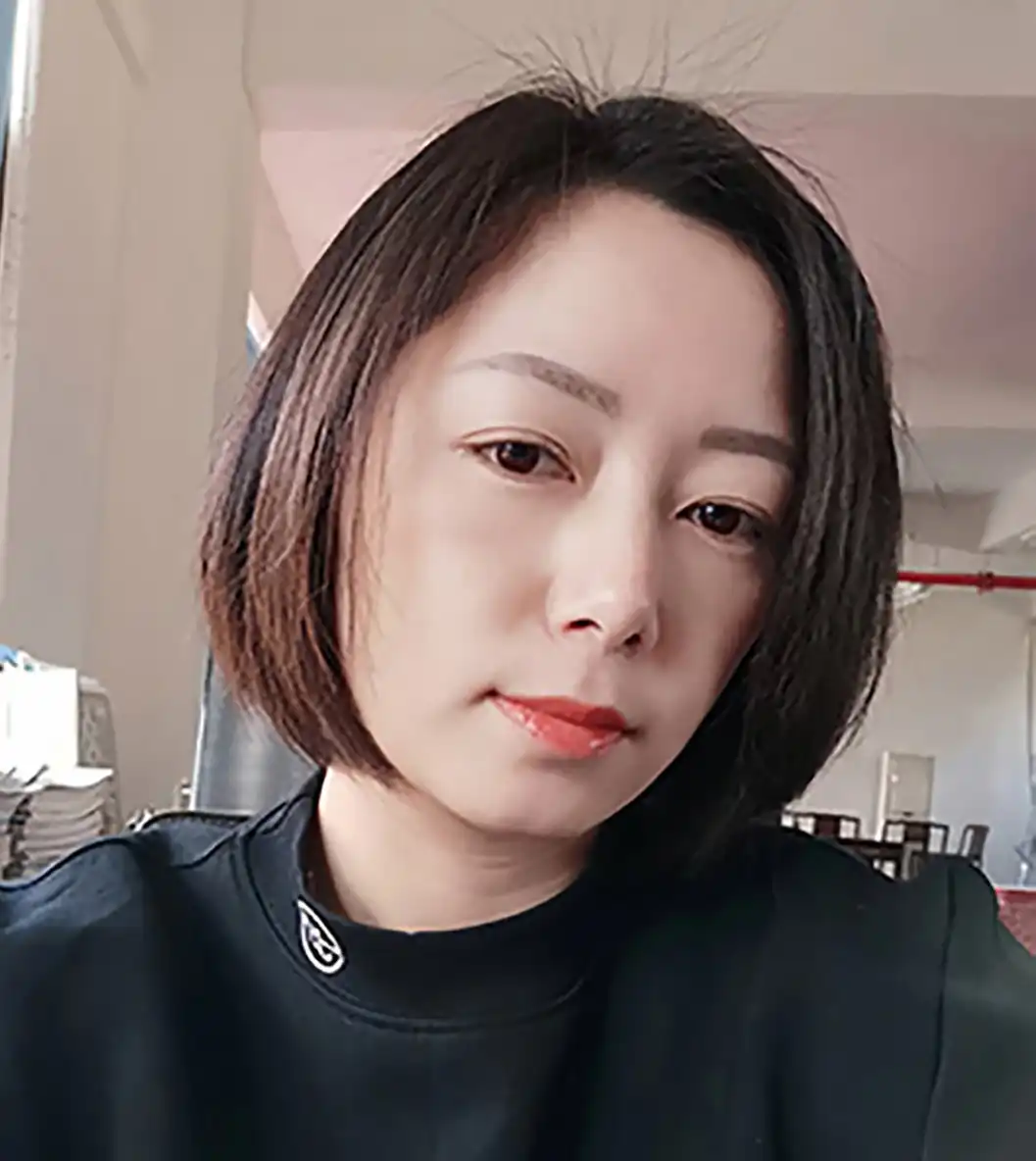
Submit the form now to get a unique quote!
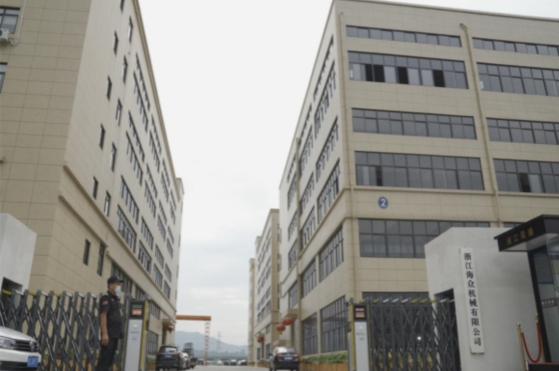
ZHEJIANG HAIZHONG MACHINERY CO., LTD.
Popular Blogs
- Successful caseProducts and services
How to Train Employees to Operate a Bottle Packing Machine Effectively?
- Successful caseIndustry insights
The Blister Packaging Process: A Complete Step-by-Step Guide
- Successful caseComparative analysisIndustry insights
What Type of PVC Is Best for Blister Packing Machines?