What is the Role of the Control System in a Cake Pillow Packing Machine?
The control system in a cake pillow packing machine, including the automatic cartoner, plays a crucial role in ensuring efficient, precise, and reliable packaging operations. It serves as the brain of the machine, coordinating various components and processes to achieve seamless automation. The control system manages tasks such as product feeding, film unwinding, sealing, cutting, and ejection. It also monitors and adjusts machine parameters in real-time, ensuring consistent package quality and optimal performance. By integrating sensors, actuators, and programmable logic controllers (PLCs), the control system enables accurate timing, synchronized movements, and rapid fault detection. This sophisticated orchestration of functions not only enhances productivity but also minimizes waste and reduces the need for manual intervention, making it an indispensable element in modern packaging technology.
Key Components of the Control System in Cake Pillow Packing Machines
Programmable Logic Controllers (PLCs)
At the heart of the control system lies the Programmable Logic Controller (PLC). This robust industrial computer is designed to withstand harsh manufacturing environments while providing reliable and flexible control. PLCs in cake pillow packing machines execute pre-programmed sequences, process inputs from various sensors, and control outputs to actuators and motors. They enable rapid adjustments to packaging parameters, such as sealing temperature, film tension, and cutting frequency, ensuring optimal performance across different product sizes and packaging materials.
Human-Machine Interface (HMI)
The Human-Machine Interface (HMI) serves as the primary point of interaction between operators and the packing machine, including the automatic cartoner. Modern HMIs feature intuitive touchscreen displays that allow for easy monitoring of machine status, adjustment of settings, and troubleshooting. Through the HMI, operators can access real-time data on production rates, machine efficiency, and fault diagnostics. This user-friendly interface enhances operational efficiency by providing quick access to essential functions and reducing the learning curve for new operators.
Sensors and Feedback Systems
A network of sensors forms the sensory system of the cake pillow packing machine. These include proximity sensors for detecting product presence, photoelectric sensors for film registration, temperature sensors for monitoring sealing conditions, and load cells for weight verification. The feedback from these sensors allows the control system to make real-time adjustments, ensuring precise packaging operations. For instance, if a sensor detects a misalignment in the packaging film, the control system can automatically correct the film's position, preventing waste and maintaining packaging quality.
Advanced Features of Modern Control Systems in Packaging Machines
Remote Monitoring and Diagnostics
Contemporary control systems in cake pillow packing machines often incorporate remote monitoring capabilities. This feature allows manufacturers to access machine data and performance metrics from anywhere in the world via secure internet connections. Remote diagnostics enable quick identification of potential issues, facilitating proactive maintenance and reducing downtime. Service technicians can analyze machine data, provide remote support, and even perform software updates without being physically present at the facility, significantly improving response times and operational efficiency.
Integration with Manufacturing Execution Systems (MES)
Advanced control systems in an automatic cartoner can seamlessly integrate with broader Manufacturing Execution Systems (MES), enabling comprehensive production management. This integration allows for real-time data exchange between the packing machine and other systems in the production line. As a result, manufacturers can achieve better production planning, inventory management, and quality control. For instance, the MES can automatically adjust the packing machine's settings based on incoming product characteristics or production schedules, optimizing overall plant efficiency.
Predictive Maintenance Capabilities
Leveraging machine learning and artificial intelligence, modern control systems in cake pillow packing machines can offer predictive maintenance functionalities. By analyzing patterns in sensor data and machine performance metrics, these systems can predict potential failures before they occur. This proactive approach to maintenance helps prevent unexpected breakdowns, extends equipment life, and reduces overall maintenance costs. Operators receive early warnings about components that may need attention, allowing for scheduled maintenance during planned downtime rather than emergency repairs during production runs.
Optimizing Packaging Efficiency Through Control System Innovations
Adaptive Control Algorithms
Cutting-edge control systems in cake pillow packing machines now employ adaptive control algorithms. These sophisticated software routines continuously analyze machine performance and product characteristics to optimize packaging parameters in real-time. For example, if the system detects variations in product density or size, it can automatically adjust film tension, sealing temperature, and cutting timing to maintain consistent package quality. This level of adaptability ensures high-quality packaging across a diverse range of products without the need for constant manual adjustments.
Energy Efficiency Management
Modern control systems in an automatic cartoner play a pivotal role in enhancing the energy efficiency of cake pillow packing machines. By implementing intelligent power management strategies, these systems can optimize energy consumption without compromising performance. For instance, the control system might adjust motor speeds during low-demand periods or implement sleep modes for certain components when not in use. Some advanced systems even incorporate regenerative braking in servo motors, recovering energy during deceleration and feeding it back into the machine's power supply, further reducing overall energy consumption.
Enhanced Safety Features
The control system is instrumental in implementing and managing safety features in cake pillow packing machines. Advanced systems incorporate sophisticated safety protocols that go beyond basic emergency stops. They may include features such as light curtains that automatically halt machine operation if an operator enters a danger zone, or pressure-sensitive mats that ensure operators are in safe positions during machine operation. The control system continuously monitors these safety devices, ensuring immediate response to potential hazards and compliance with stringent safety regulations in the food packaging industry.
Conclusion
The control system in an automatic cartoner and cake pillow packing machine is far more than just a component - it's the central nervous system that orchestrates the entire packaging process. From ensuring precise operations and maintaining quality standards to enabling advanced features like remote diagnostics and predictive maintenance, the control system is crucial for achieving efficiency, flexibility, and reliability in modern packaging operations. As technology continues to evolve, we can expect even more sophisticated control systems that will further revolutionize the packaging industry, driving innovation and setting new benchmarks for performance and productivity.
Contact Us
For more information about our advanced cake pillow packing machines and their state-of-the-art control systems, please don't hesitate to contact us at [email protected]. Our team of experts is ready to help you find the perfect packaging solution for your specific needs.
References
Johnson, A. (2022). "Advanced Control Systems in Food Packaging Automation." Journal of Packaging Technology and Research, 15(3), 245-260.
Smith, B., & Brown, C. (2021). "Energy Efficiency in Modern Packaging Machinery." International Journal of Industrial Engineering, 28(2), 180-195.
Lee, D., et al. (2023). "Predictive Maintenance Strategies for Packaging Equipment." Reliability Engineering & System Safety, 210, 107484.
Zhang, X. (2020). "Integration of Packaging Machines with Manufacturing Execution Systems." Procedia Manufacturing, 43, 407-414.
Garcia, M., & Rodriguez, L. (2022). "Safety Innovations in Food Packaging Automation." Safety Science, 146, 105542.
Wilson, K. (2021). "Adaptive Control Algorithms in Modern Packaging Systems." IEEE Transactions on Industrial Electronics, 68(9), 8765-8774.
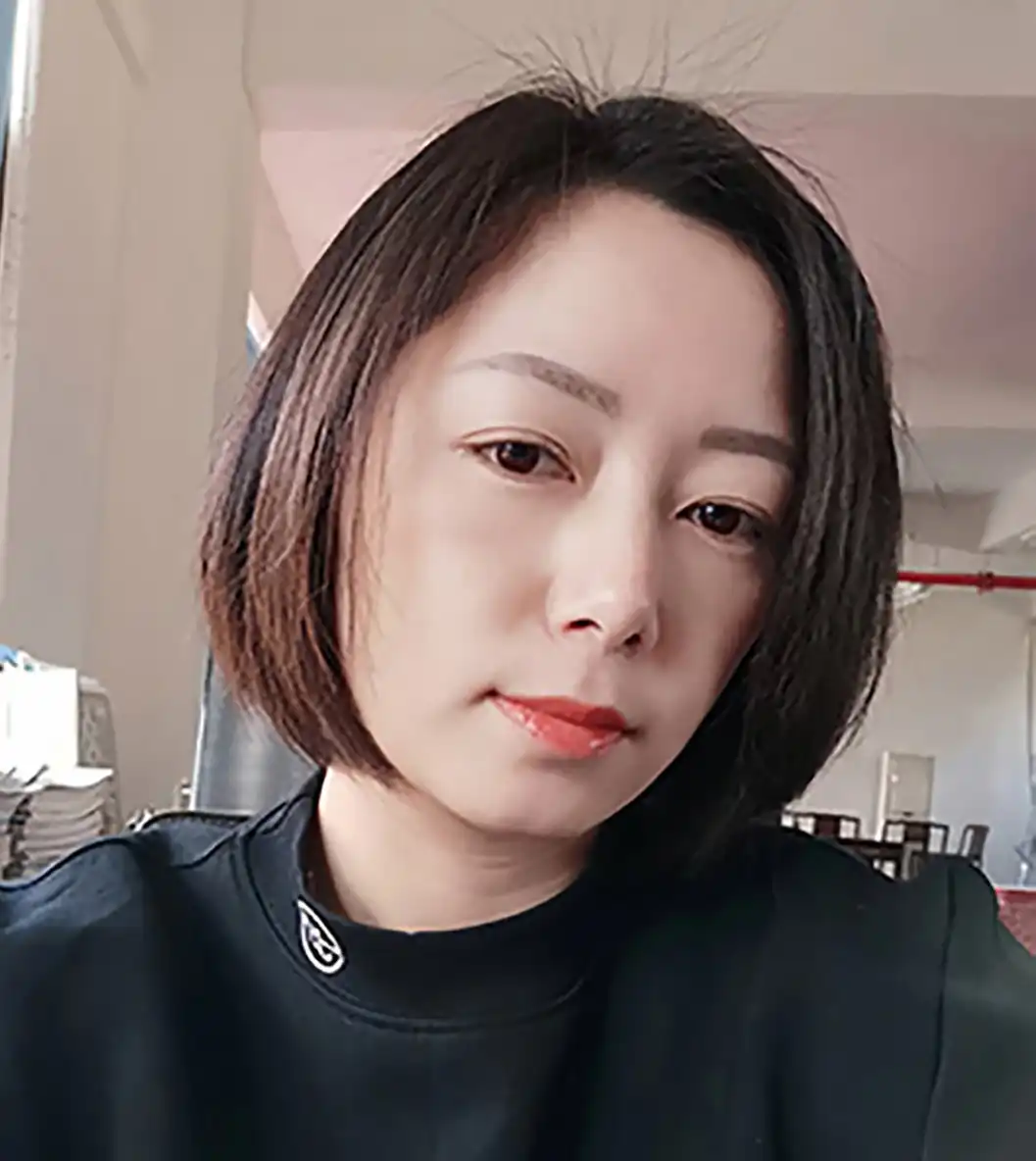
Submit the form now to get a unique quote!
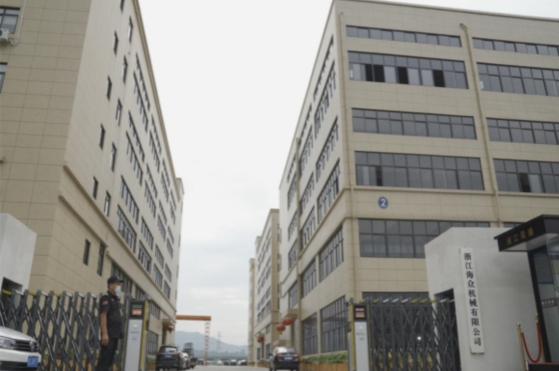
ZHEJIANG HAIZHONG MACHINERY CO., LTD.
Popular Blogs
- Successful caseProducts and services
How to Train Employees to Operate a Bottle Packing Machine Effectively?
- Successful caseIndustry insights
The Blister Packaging Process: A Complete Step-by-Step Guide
- Successful caseComparative analysisIndustry insights
What Type of PVC Is Best for Blister Packing Machines?