3 Types of Blister Packaging
Blister packaging has revolutionized the pharmaceutical industry, offering superior protection, tamper-evidence, and convenience for medication storage and dispensing. This article delves into the three primary types of blister packaging - thermoformed, cold-formed, and heat-sealed. Each type employs unique manufacturing processes and materials, typically executed using a blister packaging machine, catering to diverse pharmaceutical needs. Understanding these variations is crucial for businesses seeking optimal packaging solutions for their products. Let's explore how these innovative packaging methods enhance drug safety, extend shelf life, and improve patient compliance.
Thermoformed Blister Packaging: Precision and Versatility
The Thermoforming Process
Thermoformed blister packaging is a widely adopted solution in the pharmaceutical sector. This method involves heating a plastic film to its pliable point, then molding it into specific cavities using vacuum or pressure - typically performed by a blister packaging machine. The process allows for intricate designs and shapes, accommodating various pill sizes and forms. Typically, materials like polyvinyl chloride (PVC), polyethylene terephthalate (PET), or polypropylene (PP) are used for the forming film.
Advantages of Thermoformed Blisters
One of the primary benefits of thermoformed blister packaging is its exceptional clarity, allowing for easy product identification. This transparency not only aids pharmacists and healthcare providers but also enhances the consumer experience. Additionally, thermoformed blisters offer excellent moisture barrier properties, crucial for preserving the efficacy of moisture-sensitive medications. Produced using a blister packaging machine, this type of packaging offers the versatility needed for a wide range of pharmaceutical products, from tablets and capsules to lozenges and suppositories.
Customization and Branding Opportunities
Thermoformed blister packaging presents ample opportunities for customization and branding. Manufacturers use a blister packaging machine to incorporate unique shapes, colors, and even embossed logos into the packaging design. This level of customization not only enhances brand recognition but also aids in product differentiation on pharmacy shelves. Moreover, the ability to create child-resistant and senior-friendly designs adds another layer of versatility to thermoformed blister packaging.
Cold-Formed Blister Packaging: Superior Barrier Protection
The Cold-Forming Technique
Cold-formed blister packaging, also known as cold-sealed or pressure-formed blisters, utilizes a different approach. This method employs a ductile aluminum foil that is mechanically formed into cavities using a blister packaging machine without the application of heat. The cold-forming process creates deeper cavities compared to thermoforming, allowing for larger products or multiple doses in a single blister. The aluminum foil provides an exceptional barrier against moisture, light, and gases, making it ideal for highly sensitive medications.
Enhanced Protection for Sensitive Drugs
The superior barrier properties of cold-formed blisters make them the go-to choice for drugs that are particularly sensitive to environmental factors. Medications that are hygroscopic, photosensitive, or prone to oxidation benefit greatly from this packaging type. The aluminum foil, formed using a blister packaging machine, effectively blocks out light, moisture, and oxygen, significantly extending the shelf life of the enclosed pharmaceuticals. This level of protection is particularly crucial for biologics, enzymes, and other complex drug formulations.
Cost Considerations and Sustainability
While cold-formed blister packaging offers unparalleled protection, it comes with higher material costs compared to thermoformed options. The cold-formed blisters are produced using a blister packaging machine that shapes the aluminum foil precisely. However, the extended shelf life and reduced product waste often justify the initial investment. From a sustainability perspective, the aluminum used in cold-formed blisters is recyclable, though the recycling process may be more complex than that of plastic alternatives. Manufacturers and pharmaceutical companies must weigh these factors when selecting the most appropriate packaging solution for their products.
Heat-Sealed Blister Packaging: Balancing Simplicity and Effectiveness
The Heat-Sealing Process
Heat-sealed blister packaging represents a simpler approach compared to thermoformed and cold-formed options. In this method, pre-formed plastic blisters are filled with the product and then sealed with a lidding material using heat and pressure, typically by a blister packaging machine. The lidding material is usually a combination of aluminum foil and polymer layers, providing a balance between barrier protection and easy peel-off functionality. This packaging type is particularly popular for over-the-counter medications and supplements.
Flexibility in Production
One of the key advantages of heat-sealed blister packaging is its flexibility in production. The process, typically carried out using a blister packaging machine, requires less specialized equipment compared to thermoforming or cold-forming, making it accessible to a wider range of manufacturers. This flexibility allows for smaller production runs and quicker turnaround times, which can be particularly beneficial for seasonal medications or products with varying demand. Additionally, the simplicity of the process often translates to lower overall packaging costs.
Balancing Protection and Accessibility
Heat-sealed blisters strike a balance between product protection and consumer accessibility. While they may not offer the same level of barrier properties as cold-formed blisters, they provide sufficient protection for many pharmaceutical products. The ease of opening heat-sealed blisters makes them particularly suitable for elderly patients or those with limited dexterity. However, manufacturers must carefully consider the specific requirements of their products to ensure that heat-sealed blisters provide adequate protection throughout the product's shelf life.
Conclusion
The world of blister packaging is diverse and continually evolving to meet the complex needs of the pharmaceutical industry. Thermoformed, cold-formed, and heat-sealed blister packaging each offer unique advantages, catering to different product requirements, production scales, and market demands. These packaging types are produced using advanced blister packaging machines, which ensure precision, efficiency, and consistency in manufacturing. As pharmaceutical companies strive to enhance drug safety, extend shelf life, and improve patient compliance, the choice of blister packaging plays a crucial role. By understanding the strengths and applications of each type, businesses can make informed decisions to optimize their packaging strategies and deliver high-quality, well-protected medications to consumers worldwide.
Contact Us
For more information about our blister packaging solutions and how they can benefit your pharmaceutical products, please contact us at [email protected]. Our team of experts at Zhejiang Haizhong Machinery Co., Ltd. is ready to assist you in finding the perfect packaging solution for your unique needs.
References
Johnson, M. E., & Langdon, R. (2019). Advances in Pharmaceutical Blister Packaging Technology. Journal of Drug Delivery Science and Technology, 52, 12-24.
Smith, A. R., & Brown, L. K. (2020). Comparative Analysis of Thermoformed and Cold-Formed Blister Packaging for Moisture-Sensitive Drugs. International Journal of Pharmaceutics, 580, 119-131.
Zhang, Y., et al. (2018). Heat-Sealed Blister Packaging: A Cost-Effective Solution for Over-the-Counter Medications. Packaging Technology and Science, 31(7), 423-435.
Patel, R. M., & Thompson, K. L. (2021). Sustainability in Pharmaceutical Packaging: A Review of Current Practices and Future Directions. Sustainable Materials and Technologies, 28, e00248.
Chen, X., & Davis, G. (2017). Patient Compliance and Blister Packaging Design: A Correlation Study. Drug Development and Industrial Pharmacy, 43(8), 1262-1272.
Lopez-Rubio, A., & Lagaron, J. M. (2022). Novel Materials for Advanced Blister Packaging in the Pharmaceutical Industry. Progress in Materials Science, 124, 100875.
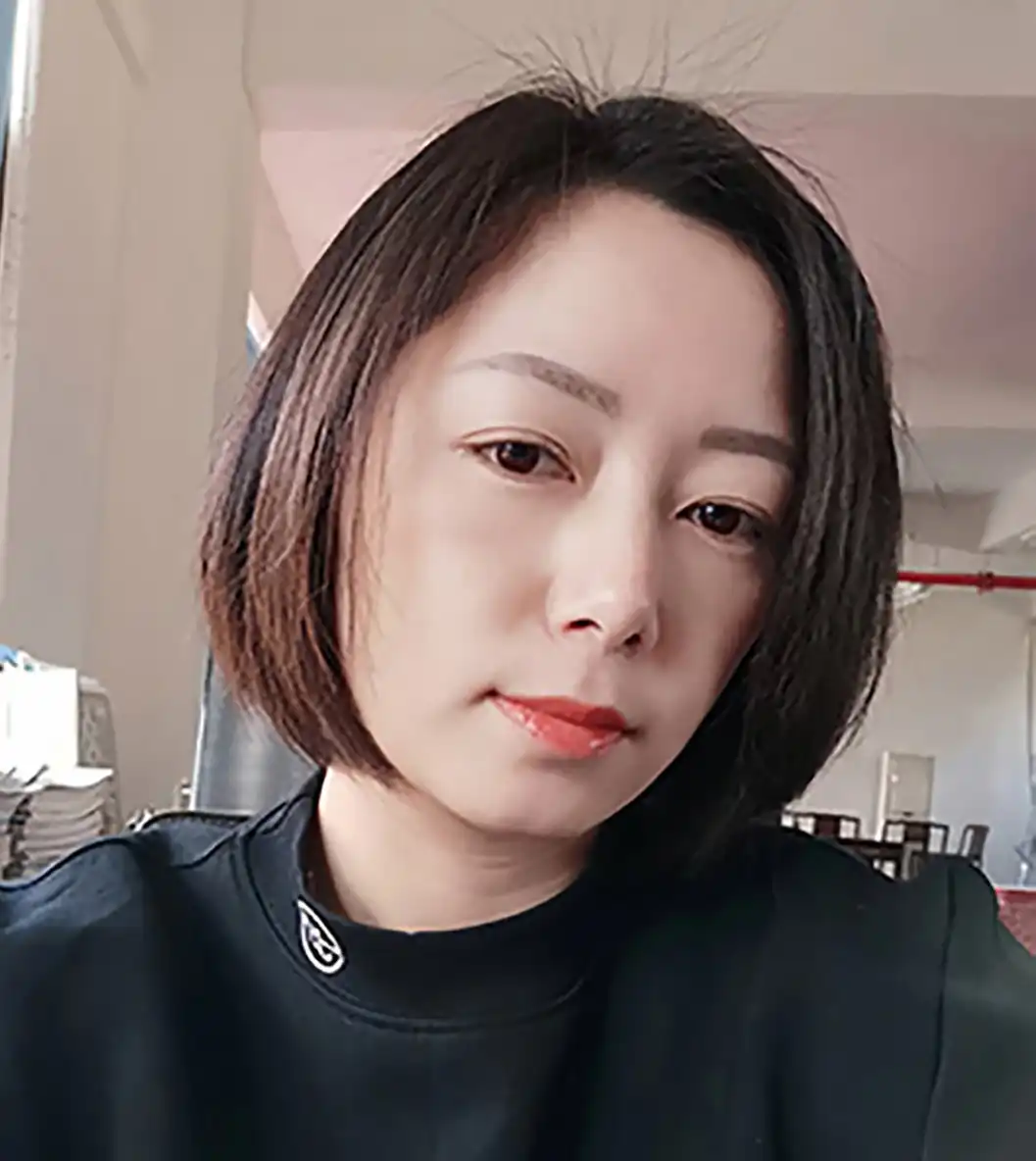
Submit the form now to get a unique quote!
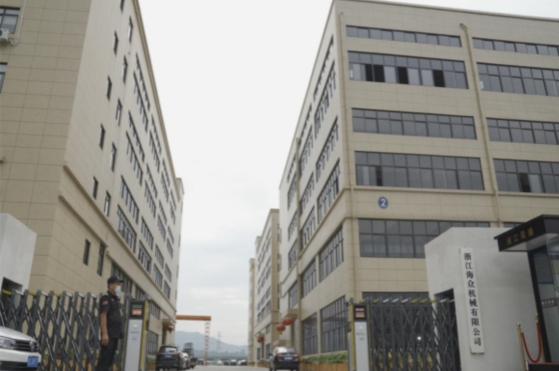
ZHEJIANG HAIZHONG MACHINERY CO., LTD.
Popular Blogs
- Successful caseProducts and services
How to Train Employees to Operate a Bottle Packing Machine Effectively?
- Successful caseIndustry insights
The Blister Packaging Process: A Complete Step-by-Step Guide
- Successful caseComparative analysisIndustry insights
What Type of PVC Is Best for Blister Packing Machines?