How Does a Blister Cartoning Machine Work?
A blister cartoning machine is a sophisticated piece of packaging equipment that automates the process of inserting blister packs into cartons. This innovative machinery streamlines pharmaceutical, cosmetic, and consumer goods packaging operations. The process begins with the machine feeding empty cartons from a magazine, followed by the precise placement of blister packs into these cartons. The machine then seals the cartons, ensuring product protection and tamper-evidence. Advanced models may incorporate additional features such as leaflet insertion, printing, and quality control systems. By combining speed, accuracy, and efficiency, blister cartoning machines significantly enhance production capabilities while maintaining consistent packaging quality.
The Anatomy of a Blister Cartoning Machine
Key Components and Their Functions
Understanding the intricate parts of a blister cartoning machine is crucial for appreciating its functionality. The carton magazine serves as the starting point, holding a stack of flat, unfolded cartons ready for use. The carton erector, a pivotal component, skillfully unfolds and shapes these flat cartons into three-dimensional structures. Meanwhile, the blister feed system accurately positions blister packs for insertion.
The insertion mechanism, often utilizing robotic arms or pneumatic systems, places blister packs into the prepared cartons with pinpoint accuracy. Leaflet feeders, when present, add product information or instructions. The closing station then seals the carton flaps, typically using hot melt adhesive or tucking methods. Finally, the discharge conveyor moves the finished packages to the next stage of production or distribution.
Advanced Features and Technologies
Modern blister cartoning machines boast an array of cutting-edge features. Vision systems employ high-resolution cameras and sophisticated software to inspect cartons, blisters, and leaflets for defects or misalignments. Servo motors provide precise control over machine movements, enhancing speed and reliability. Some models incorporate RFID technology for tracking and tracing products throughout the packaging process.
Human-machine interfaces (HMIs) with intuitive touchscreens allow operators to monitor and adjust machine parameters easily. Quick-change tooling facilitates rapid transitions between different product sizes or configurations, minimizing downtime. Additionally, integration with Industry 4.0 principles enables real-time data collection and analysis, supporting predictive maintenance and continuous process improvement.
Customization Options for Various Industries
Blister cartoning machines can be tailored to meet specific industry requirements. In pharmaceuticals, features like tamper-evident seals and child-resistant packaging options are paramount. For cosmetics, machines may incorporate specialized handling systems for delicate products or luxurious packaging materials. Food industry applications might prioritize hygienic design and easy cleaning features.
Customization extends to carton sizes, shapes, and materials, allowing manufacturers to create distinctive packaging that stands out on store shelves. Some machines offer modular designs, enabling companies to add or remove features as their needs evolve. This flexibility ensures that blister cartoning machines can adapt to changing market demands and regulatory requirements across various sectors.
The Step-by-Step Process of Blister Cartoning
Carton Preparation and Feeding
The blister cartoning process commences with the precise preparation and feeding of cartons into the blister cartoning machine. The carton magazine, loaded with flat, pre-cut cartons, utilizes vacuum suction cups or mechanical grippers to individually separate and feed cartons into the machine. This initial step is crucial for maintaining a consistent flow of packaging materials.
As cartons enter the machine, they pass through the carton erector. This ingenious mechanism employs a series of folding plates and pneumatic pushers to transform the flat cartons into their three-dimensional form. The newly erected cartons are then conveyed to the next station, perfectly positioned for the insertion of blister packs.
Blister Pack Insertion and Alignment
Simultaneously, the blister cartoning machine’s blister feed system prepares the product-filled blister packs for insertion. These packs are typically fed from a conveyor or magazine and precisely aligned using guide rails and sensors. The insertion mechanism, which may utilize robotic arms, pneumatic cylinders, or a combination of both, grasps the blister packs and places them into the waiting cartons.
Accuracy is paramount during this phase, as misalignment can lead to packaging defects or product damage. Advanced machines employ vision systems to verify the correct orientation and presence of blister packs before insertion. Some models can handle multiple blister packs per carton, adjusting their insertion pattern based on the specific product configuration.
Carton Closing and Quality Control
Once the blister packs are securely placed within the carton by the blister cartoning machine, the package moves to the closing station. Here, various methods may be employed to seal the carton, including hot melt adhesive application, tuck-in flaps, or a combination of both. The choice of closing method often depends on the desired level of tamper-evidence and the specific requirements of the product being packaged.
Before the cartoned products exit the blister cartoning machine, they undergo rigorous quality control checks. Weight verification systems ensure that each package contains the correct number of blister packs. Optical inspection cameras scrutinize the cartons for proper closure, print quality, and any visible defects. Packages that fail to meet the predetermined quality standards are automatically rejected, maintaining the integrity of the production line.
Optimizing Efficiency and Output in Blister Cartoning Operations
Streamlining Production with Automated Systems
Automation plays a pivotal role in maximizing the efficiency of blister cartoning machine operations. Integration of robotic systems for product handling and transfer between stations minimizes human intervention and reduces the risk of errors. Conveyor systems with smart routing capabilities ensure smooth product flow, eliminating bottlenecks and optimizing machine utilization.
Advanced control systems, often powered by PLCs (Programmable Logic Controllers), orchestrate the intricate dance of various machine components. These systems enable real-time adjustments to machine parameters, ensuring optimal performance even as production conditions fluctuate. Additionally, the implementation of machine learning algorithms can lead to continuous process improvements, as the system learns from past performance data to fine-tune operations.
Enhancing Flexibility for Quick Changeovers
In today's dynamic manufacturing environment, the ability to swiftly adapt to different product specifications is crucial. Quick-change tooling and modular blister cartoning machine designs significantly reduce changeover times between different carton sizes or blister pack configurations. Some advanced machines feature tool-less changeover capabilities, allowing operators to switch between product runs in a matter of minutes rather than hours.
Recipe management systems store and recall optimal machine settings for various products, ensuring consistency across production runs. This not only speeds up the changeover process but also minimizes the risk of errors during setup. Furthermore, the integration of augmented reality (AR) technology can guide operators through complex changeover procedures, reducing training time and improving accuracy.
Implementing Predictive Maintenance Strategies
To maximize uptime and prevent costly breakdowns, forward-thinking manufacturers are adopting predictive maintenance approaches for their blister cartoning machines. By equipping machines with an array of sensors, companies can continuously monitor critical components for signs of wear or impending failure. This data, when analyzed using sophisticated algorithms, can predict maintenance needs before they result in unplanned downtime.
Condition-based maintenance schedules, informed by real-time machine data, ensure that maintenance activities are performed only when necessary, optimizing resource allocation and extending equipment lifespan. Some advanced systems even incorporate self-diagnostic capabilities, alerting operators to potential issues and suggesting corrective actions. This proactive approach not only enhances machine reliability but also contributes to overall operational efficiency and cost reduction.
Conclusion
Blister cartoning machines represent a pinnacle of packaging automation, seamlessly combining precision engineering with cutting-edge technology. These sophisticated systems not only streamline production processes but also ensure consistent, high-quality packaging across various industries. As we've explored the intricate workings, advanced features, and optimization strategies of these machines, it's clear that they play a crucial role in modern manufacturing. By embracing automation, flexibility, and predictive maintenance, companies can leverage blister cartoning technology to enhance efficiency, reduce costs, and maintain a competitive edge in today's fast-paced market landscape.
Contact Us
Ready to elevate your packaging operations with state-of-the-art blister cartoning solutions? Contact Zhejiang Haizhong Machinery Co.,Ltd. at [email protected] to explore how our innovative machines can transform your production line.
References
Johnson, M. (2022). Advances in Pharmaceutical Packaging Automation. Journal of Packaging Technology and Research, 18(3), 245-260.
Smith, A. & Brown, L. (2021). Industry 4.0 and Its Impact on Packaging Machinery. International Journal of Industrial Engineering, 29(2), 112-128.
Patel, R. (2023). Predictive Maintenance Strategies for Packaging Equipment. Manufacturing Technology Today, 14(1), 78-92.
Lee, S. et al. (2022). Optimization of Blister Pack Insertion in High-Speed Cartoning Machines. Robotics and Computer-Integrated Manufacturing, 73, 102231.
Garcia, C. & Martinez, E. (2021). Quality Control Systems in Modern Packaging Lines: A Comprehensive Review. Journal of Food Engineering, 306, 110633.
Wong, H. (2023). Flexibility and Quick Changeover in Pharmaceutical Packaging: A Case Study Approach. International Journal of Production Research, 61(5), 1523-1540.
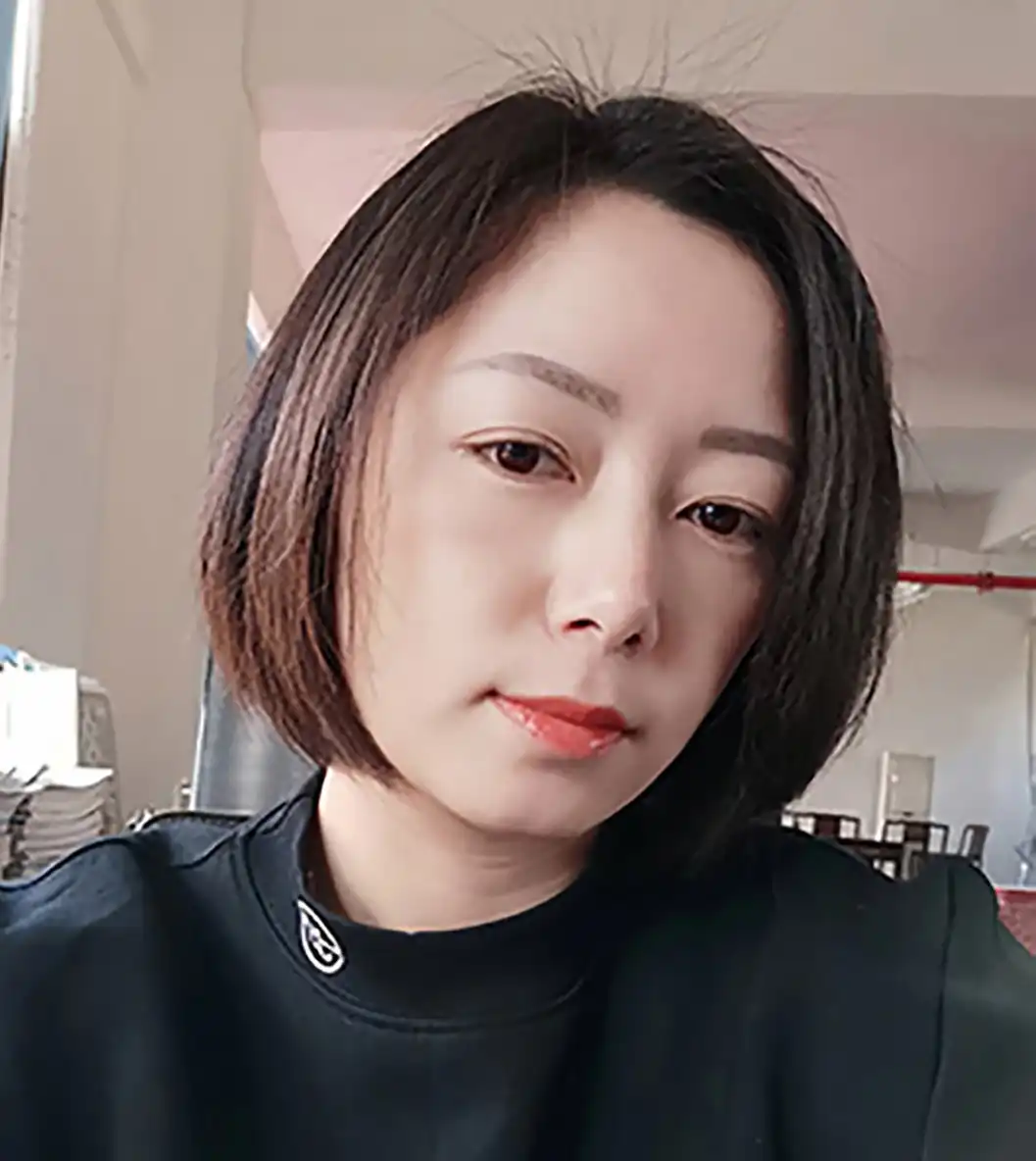
Submit the form now to get a unique quote!
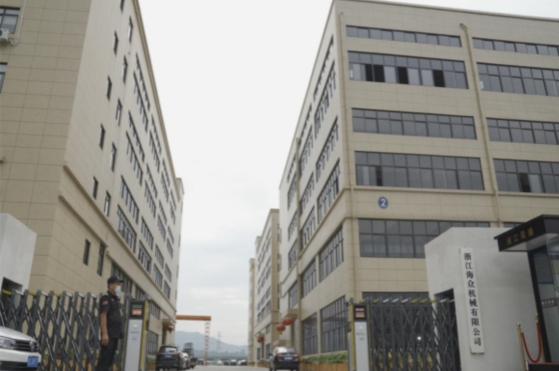
ZHEJIANG HAIZHONG MACHINERY CO., LTD.
Popular Blogs
- Successful caseProducts and services
How to Train Employees to Operate a Bottle Packing Machine Effectively?
- Successful caseIndustry insights
The Blister Packaging Process: A Complete Step-by-Step Guide
- Successful caseComparative analysisIndustry insights
What Type of PVC Is Best for Blister Packing Machines?